Создание деталей для машин «Формулы-1» – настоящая наука: их моделируют и выпекают по сложным правилам
Это вторая часть материала об изготовлении деталей для машин «Формулы-1». Это перевод статьи Пэта Симондса в журнале F1 Racing UK за июль 2019 года. Сегодня обратимся непосредственно к процессу создания и производства аэродинамических частей машин.

В то время как процесс изготовления металлических компонентов при помощи литья, обработки и даже 3D печати относительно хорошо известен, процесс производства композитных материалов представляется весьма сложным и загадочным. Что ж, попробуем приоткрыть завесу тайны происходящего при их создании.
Деталь из композитного материала может иметь одну из двух форм. Первая: твердая монолитная, относительно тонкая структура, такая как воздуховод тормозов, где слои углеродного волокна скрепляются вместе, чтобы создать изделие, которое напоминает что-то, сделанное из листового металла. Второй, более частый, вариант – это композитная структура, состоящая из двух тонких оболочек, разделенных материалом сердцевины, который обычно представляет собой структуру из сот, но также может быть очень легкой пеной.
Процесс изготовления композитного материала начинается, как и следовало ожидать, в системе автоматизированного проектирования (САПР). Разработка начинается с 3D модели конечной детали, характеристики которой будут меняться в процессе проектирования и анализа силового воздействия на компонент. Инженер-разработчик выбирает тип волокна и смолы, сколько должно быть нитей в пучке и как эти пучки сплетать между собой.
3D-модель является основой для создания образца, по которому далее будет изготовлена форма для отливки детали. Этот образец является живым представлением будущей детали. Обычно он изготавливается из материала, использующего эпоксидную смолу. Инженер далее загружает модель из САПР в специальный 5-осевой станок, который потом вырезает деталь именно той формы, которая требуется.
После обработки поверхность детали должна быть доведена до блеска. Это все еще в значительной степени выполняется путем шлифования вручную влажной и сухой тканью с последующим нанесением глянцевой эпоксидной краски. Этот образец далее исследуется при помощи лазерного сканирования или специальной сканирующей 3D-машины, ведь каждая ошибка в шаблоне будет воспроизводиться и в самих деталях.
Следующий шаг – это создание самой формы для отливки. Она изготавливается из карбона, что может показаться расточительством, но факт в том, что под воздействием температуры, форма будет расширяться так же, как будет потом формироваться и расширяться итоговая карбоновая деталь внутри этой формы. Предварительно пропитанное волокно может являться более дешевым вариантом, хоть оно и будет многослойным, чтобы форма была достаточно жесткой. Если форма большая, например, для монокока, в заготовку будет встроена рамка жесткости. После первоначального отвердевания форма будет крепкой, но затем она будет подвергаться обработке при более высокой температуре, чтобы повысить прочность для дальнейшего использования.
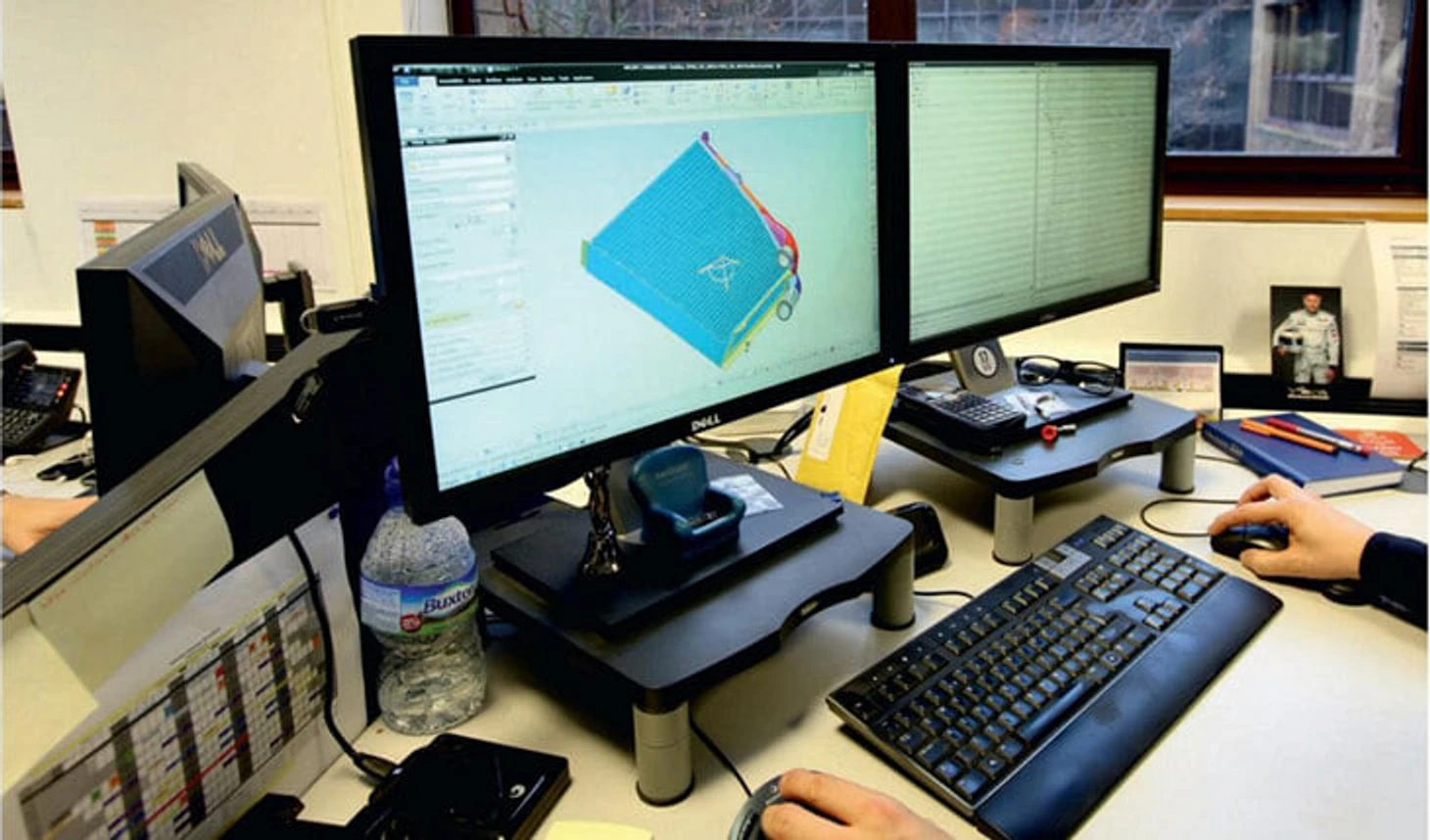
Все начинается с компьютерного моделирования
Когда закончены формы для отливки, можно начинать производство конечной детали. На первом этапе надо поместить предварительно пропитанное смолой волокно в форму. Это делается высококлассными инженерами, которые строго следуют заданию, которое создал разработчик и которое проверили инженеры при помощи стресс-тестов. Ориентация пучков волокна имеет важнейшее значение, так что иногда приходится экспериментировать во время их укладки в форму. Волокно может неохотно укладываться в острые углы формы, поэтому инженеры используют обычный домашний фен для волос, чтобы нагреть материал и сделать его более податливым.
Несколько слоев могут формироваться именно таким образом. Каждый из них должен быть уложен так, как описано в техническом задании, и иногда лазеры и системы дополненной реальности помогают инженеру укладывать пучки более точно. Обязательно нужно убедиться в том, что между слоями нет воздуха. Это достигается путем откачивания воздуха и умеренного нагревания, которые укрепляют слои и укладывают волокно точнее в форму.
Когда готовы все слои, можно приступать к последнему этапу. Сначала углеродное волокно в форме покрывается разделительной пленкой. Она, в свою очередь, покрывается хлопчатобумажной дышащей тканью, а та – вакуумным мешком, который запечатывается в форму с помощью шпатлевки. Линии соединения проталкиваются через вакуумный мешок, а вся сборка помещается в автоклав – по сути, это огромную печь, где можно осуществлять нагрев под давлением. После этого начинается процесс затвердевания. При этом температура и давление строго контролируются. Это двухступенчатый процесс, когда при определенной температуре смола становится текучей и воздух выходит из материала, а затем нити скрепляются, и все изделие окончательно обретает форму. Во время обработки температура в автоклаве поднимается до 175оС, а давление достигает 6 бар. Такие показатели удерживаются какое-то время, затем температура и давление снижаются.

Встроенная рамка жесткости для детали большого размера, например, монокока
Если планируется использование еще одного материала в сердцевине будущего изделия между слоями углеродного волокна, то есть два способа его туда поместить: первый – одновременно «запечь» внешний слой, сердцевину и внутренний слой; второй – слить сердцевину и предварительно подготовленный внешний слой. Специальное клеящее вещество в виде пленки будет помещено между материалом сердцевины и слоями углеродного волокна, чтобы скрепить их вместе.
Чтобы материал выдерживал больше нагрузок, специальные вставки тоже должны быть встроены в структуру. Это могут быть алюминий или твердый углепластик, а для скрепления между сердцевиной и слоями углеродного волокна может использоваться пенообразный клей.
Перед тем как пройти верификацию готовое изделие после охлаждения достается из формы и очищается. Если это, например, антикрыло или элемент подвески, то деталь должна быть проверена ультразвуковым сканированием или рентгеновским аппаратом на предмет отсутствия структурных проблем. Затем ее проверяют на прочность, а уже потом устанавливают на машину.
Появление композитных материалов и развитие технологий их производства позволили сделать материалы для машин крепче и легче, а сами машины – безопаснее. Да, углеродное волокно было изобретено в авиационной отрасли, но его основное развитие и широкое применение стали возможным благодаря автоспорту. Ведь сейчас композитные материалы применяют и в гражданском автомобилестроении – для облегчения машин и их топливной эффективности.
Фото: F1 Racing UK
Этот блог в соцсетях, будьте в курсе новых статей:
https://twitter.com/OnMaxSpeed
https://t.me/onmaxspeed
Фото: globallookpress.com/Hoch Zwei