Есть ли альтернативы углеродному волокну?
Когда Формула 1 объявила, что она стремится стать углеродно-нейтральной к 2030 году, основной фокус был на топливе для гоночных машин. Но оно составляет всего 0,7% от примерно 250000 тонн CO2, которые «оставляет за собой» чемпионат. Куда больший след оставляет транспортировка людей и оборудования по всему земному шару, и это тоже находится в повестке и обсуждается экспертами. В этот процесс включены люди из авиационной отрасли, а также академия, которая занимается разработкой нового авиационного топлива.
Многие указывают на то, что машины сами по себе строятся из большого количества углеродных материалов, и справедливо спрашивают, как это отражается на стремлении серии стать углеродно-нейтральной и ведется ли поиск альтернатив.
Здесь стоит упомянуть, что мы подразумеваем под углеродным волокном или, если быть точнее, под композитами из углеродного волокна. Эти материалы состоят из углеродного волокна, которое вплетено в ткань и пропитано смолой. В необработанном состоянии смола держит волокна вместе, но там остается возможность вплести в форму еще и ткань. Обычно структура состоит из нескольких кусков ткани, которые в свою очередь разделяются стабилизатором в виде сот, чтобы поддерживать геометрическую форму. После термальной обработки смола застывает, и структура становится прочным элементом.

Существует много типов углеродных волокон, и они могут быть соединены разными способами, но в Ф1 используются полиакрилонитриловые волокна. Они так называются, потому что прекурсором для них является полимер полиакрилонитрил. Это органический материал, который скручивают в волокна, а затем стабилизируют химическим путем. В этот момент волокна еще белые, но затем идет карбонизация, которая происходит при высокой температуре и превращает волокна в плотно соединенные углеродные кристаллы. После этого применяется графит при 3000 градусах. Затем их собирают вместе и скручивают в ту форму, которая требуется.
Углерод может принимать разные формы, или, как говорят химики, разные аллотропные модификации. Он может быть как в виде мягкого графита, так и в виде прочнейшего кристалла. Углерод в волокне может быть как прочным, так и жестким. Именно это сделало его таким привлекательным материалом для создания легких и прочных изделий. Изначально такие материалы разработали для Британских ВВС в Фарнборо и стали применять в аэропромышленности в 1960-х. Но именно автоспорт показал, как можно его разнообразно и гибко использовать. Конечно, в 1960-х никто особо не задумывался об углеродном следе при производстве, сейчас же идут исследования по поиску замены углеродных волокон и смол, которые тоже создаются на основе углеводородов.
Нет ничего нового в том, чтобы сочетать жесткость и прочность при использовании волокон и смол. Стекловолокно используется в конструкции кузова машин уже много лет и исповедует те же принципы, что и при постройке домов из деревянных материалов, скрепленных жидкой (впоследствии застывшей) субстанцией. Такой метод строительства домов в Европе известен с XII века: деревянная решетка и клейкая субстанция, похожая на глину, используются так же, как и обработанная при комнатной температуре смола в современных материалах.
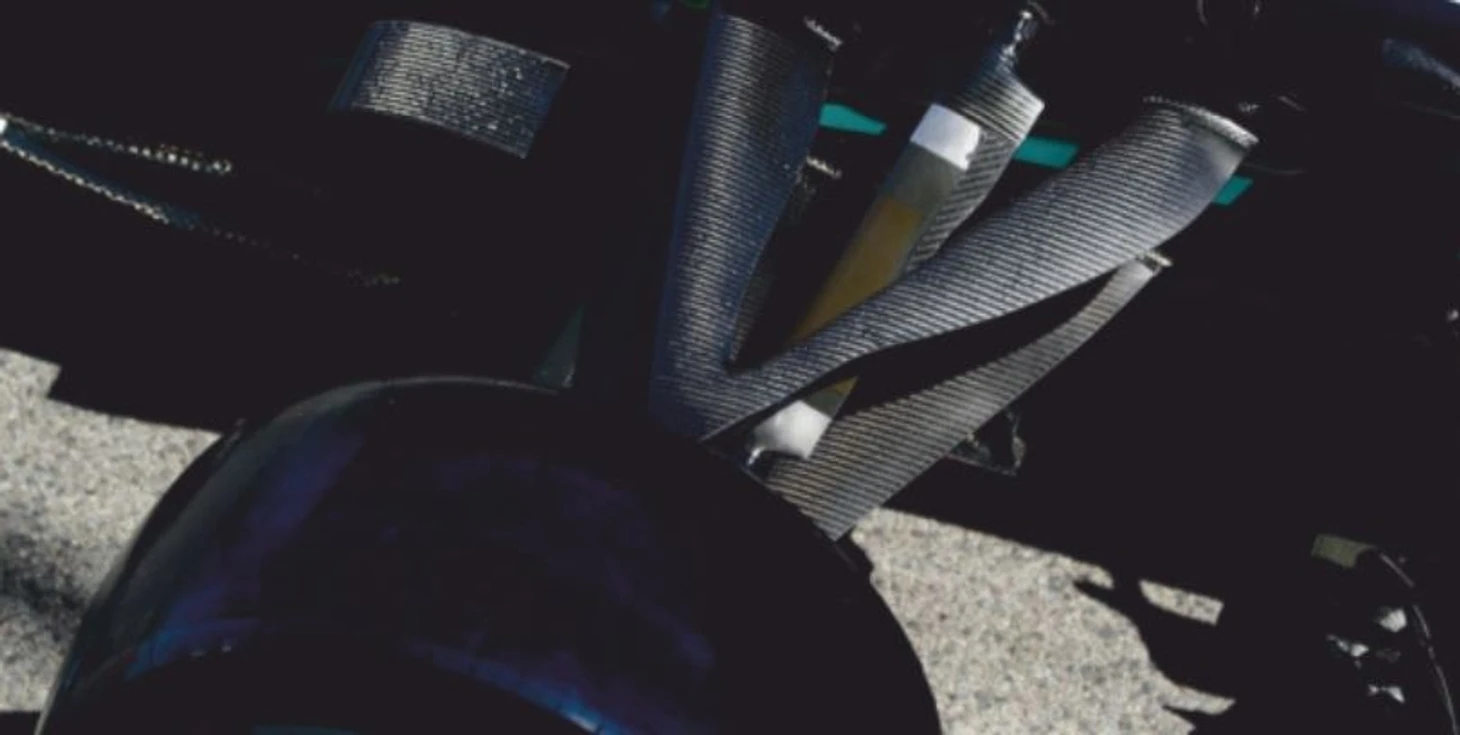
Идея биокомпозитных материалов не нова, но пока биоматериалы используют как часть композитов, удивительные свойства углеродных соединений стали еще более очевидны. Современные биокомпозиты сделаны из натуральных волокон, обычно льна, но также используются конопля и джут. Так как они имеют естественное происхождение, их считают экологичными, но, как и с биотопливом, если используются плодородные почвы для их выращивания, они начинают конкурировать с производством еды. В целом производство биологических волокон менее энергозатратно, чем синтетических, к тому же они менее вредны для окружающей среды и их легче утилизировать. Смолы тоже могут быть естественного происхождения и их вариант, созданный из остатков еды, имеет высокую температуру перехода, что подходит для многих компонентов.
Так насколько меньше выбросов от производства и использования натуральных композитов по сравнению с синтетическими? К сожалению, на этот вопрос легко ответить не получится. Механические свойства натуральных волокон не так хороши, как у углерода, и, хотя у производителей есть интересные способы уменьшения этого недостатка, компонент из льняного композита будет тяжелее своего углеродного аналога. Когда говорят, что углеродный след натурального композита того же веса, что и углеродного, меньше на 75%, то в расчет не берут разницу в весе финального изделия, чтобы добиться сопоставимой жесткости и прочности. Как не берутся в расчет другие материалы и процессы изготовления.
Да, это может звучать пессимистично, но это не так. Маловероятно, что натуральные композиты будут использоваться для компонентов, требующих высокой жесткости и прочности (таких как монокок или рычаги подвески), но есть области, где снижение этих качеств непринципиально. Я думаю, в будущем мы увидим больше деталей из натуральных композитов, а их качество и свойства будут улучшаться, как улучшались с годами постоянного развития углеродные композиты. На это будут влиять усовершенствования процессов изготовления или даже генная инженерия растений, из которых такие биокомпозиты изготавливаются.
Это перевод статьи Пэта Симондса из журнала GP Racing UK за август 2022.
Фото: MotorsportImages.com;
Этот блог в соцсетях: