Как делают шлемы «Ф-1»: материал из космической промышленности крепче корпуса болида, «внутренности» крепят вручную
Современные шлемы «Формулы-1» – произведение технического искусства и суперзащита. Они спасают головы пилотов, не плавятся при температурах до 790 градусов по Цельсию и по последним требованиям безопасности обязаны выдерживать нагрузку, эквивалентную выстрелу из дробовика в визор – как вам такое?
Но как же их делают? Из каких суперматериалов и где? Может, в тайной гигафабрике?
Бахрейн для «Формулы-1» – в первую очередь трасса «Сахир»: дом для местного этапа, но мало кто знает, что здесь же расположена фабрика компании Bell, производящей шлемы сразу для 13 из 20 гонщиков серии. Вот она, прямо напротив автодрома.
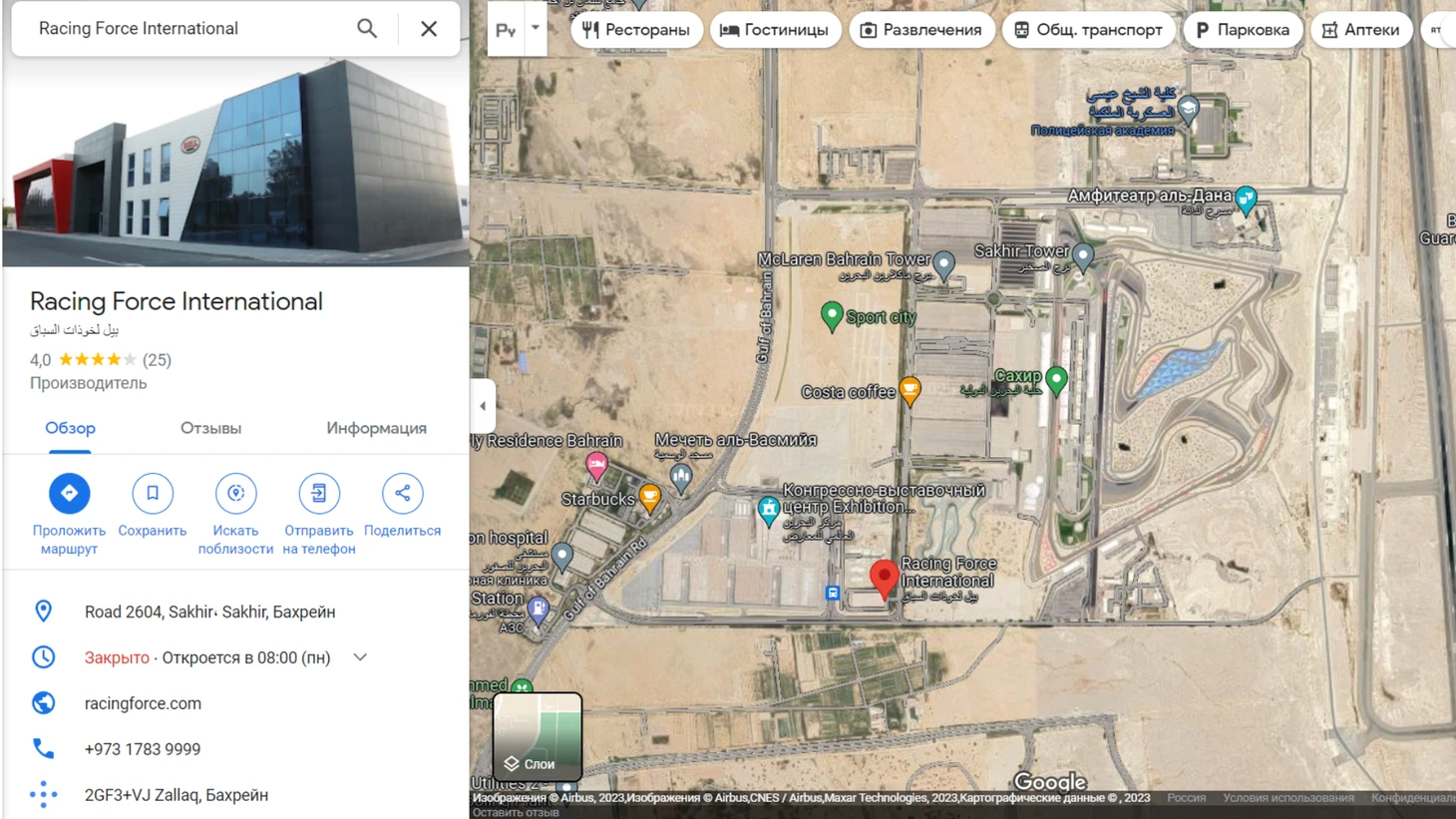

Bell основана в 1954-м году и не раз становилась настоящим новатором на протяжении истории разработки гоночных шлемов. Сейчас бренду принадлежат порядка 70% всего рынка и его с уверенностью можно назвать крупнейшим и известнейшим производителем защитной экипировки гонщиков.
Давайте заглянем на их завод, чтобы узнать, как и из чего производят современную защиту.
В день Bell собирает 180 шлемов для всех гоночных серий – включая сувенирные реплики. Каждый в зависимости от модели может состоять из 60-100 элементов.
Начинается производство в отделе «пенопласта и впрысков пластиков». Вот эти шарики, изготовленные из вспененного полистирола, заливаются в специальные формы и превращаются во внутренности шлема.
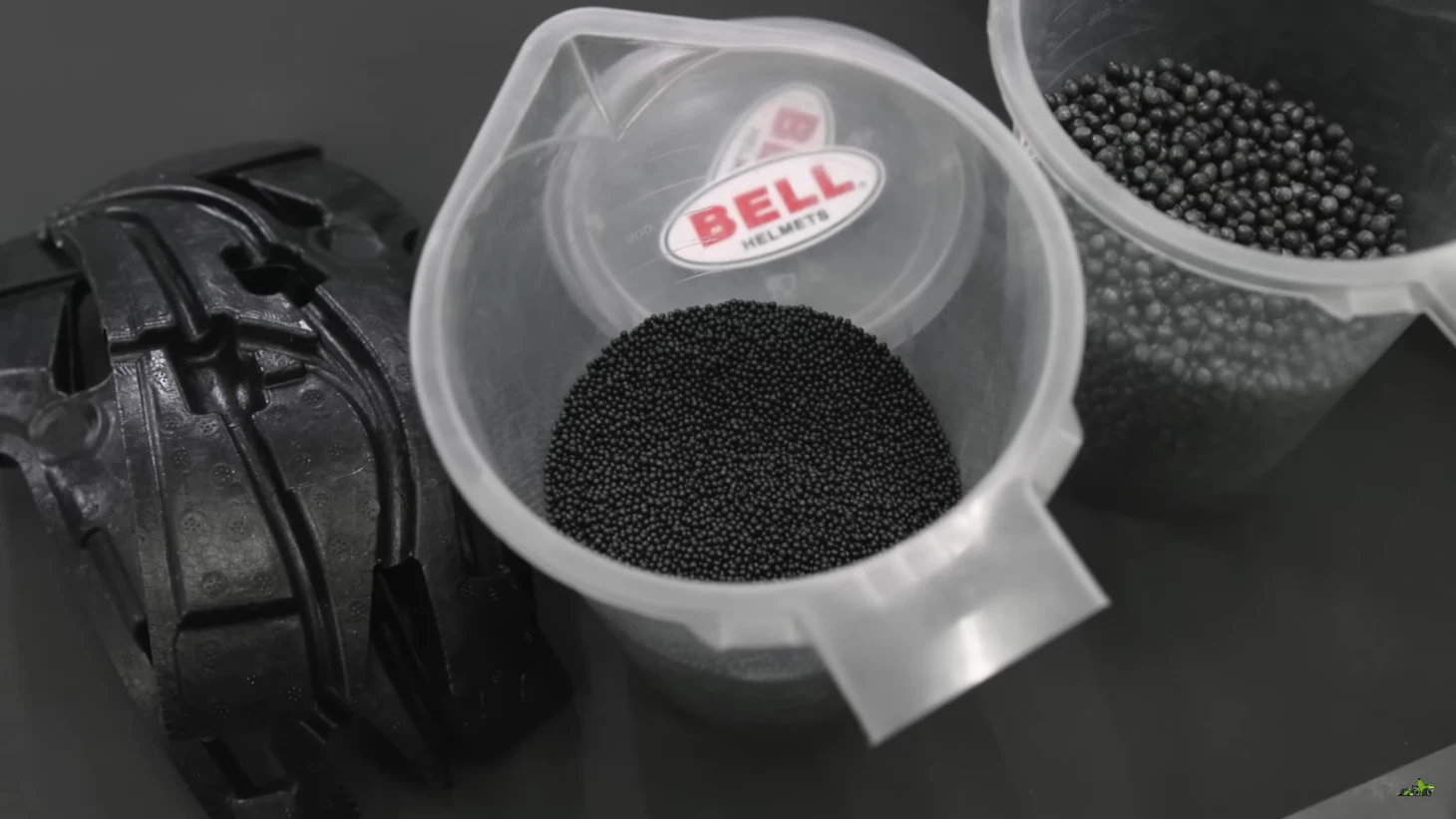
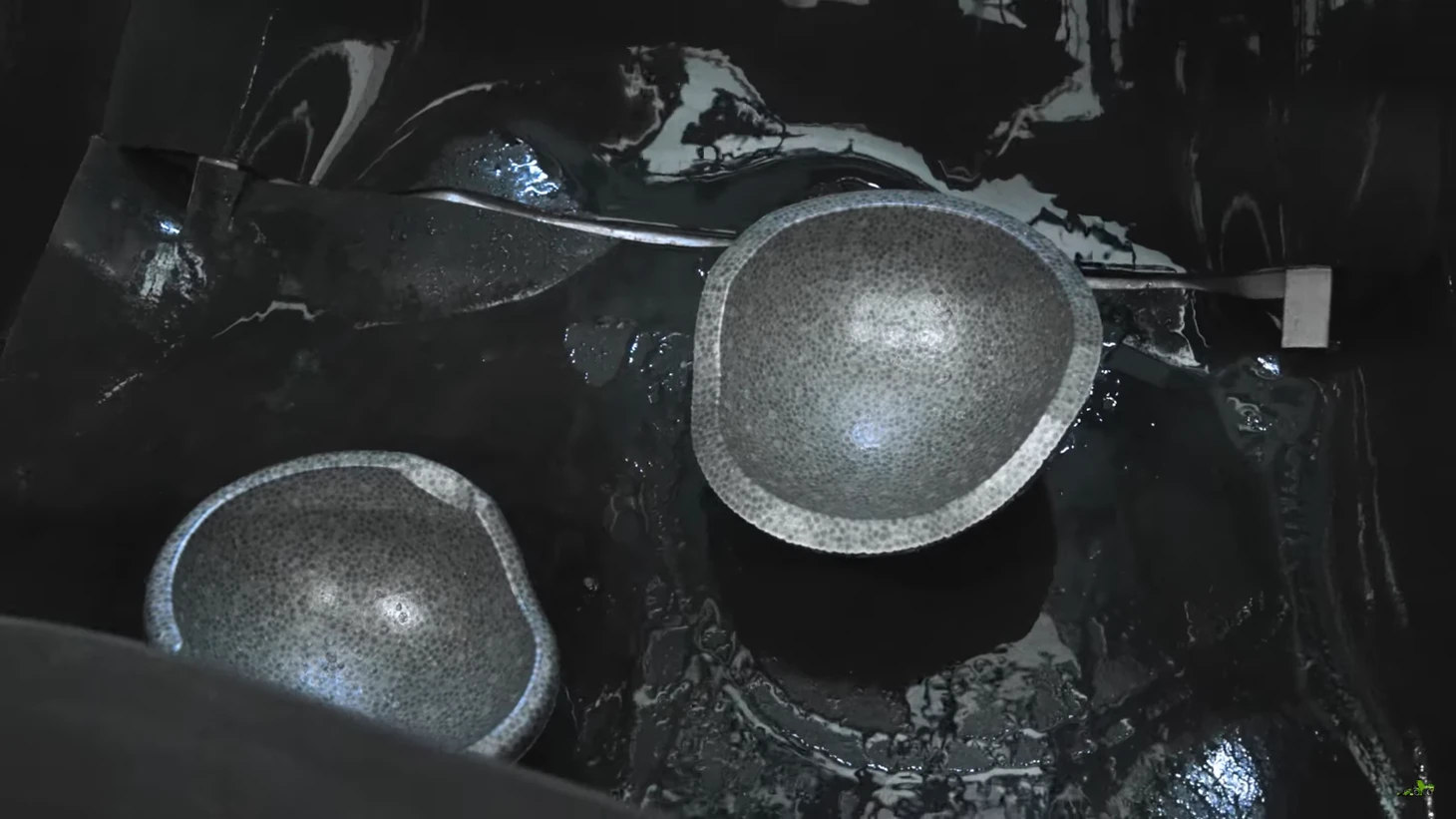
Бусинки из полистирола отличаются размером и жесткостью. Для разных частей шлема используют свой материал.
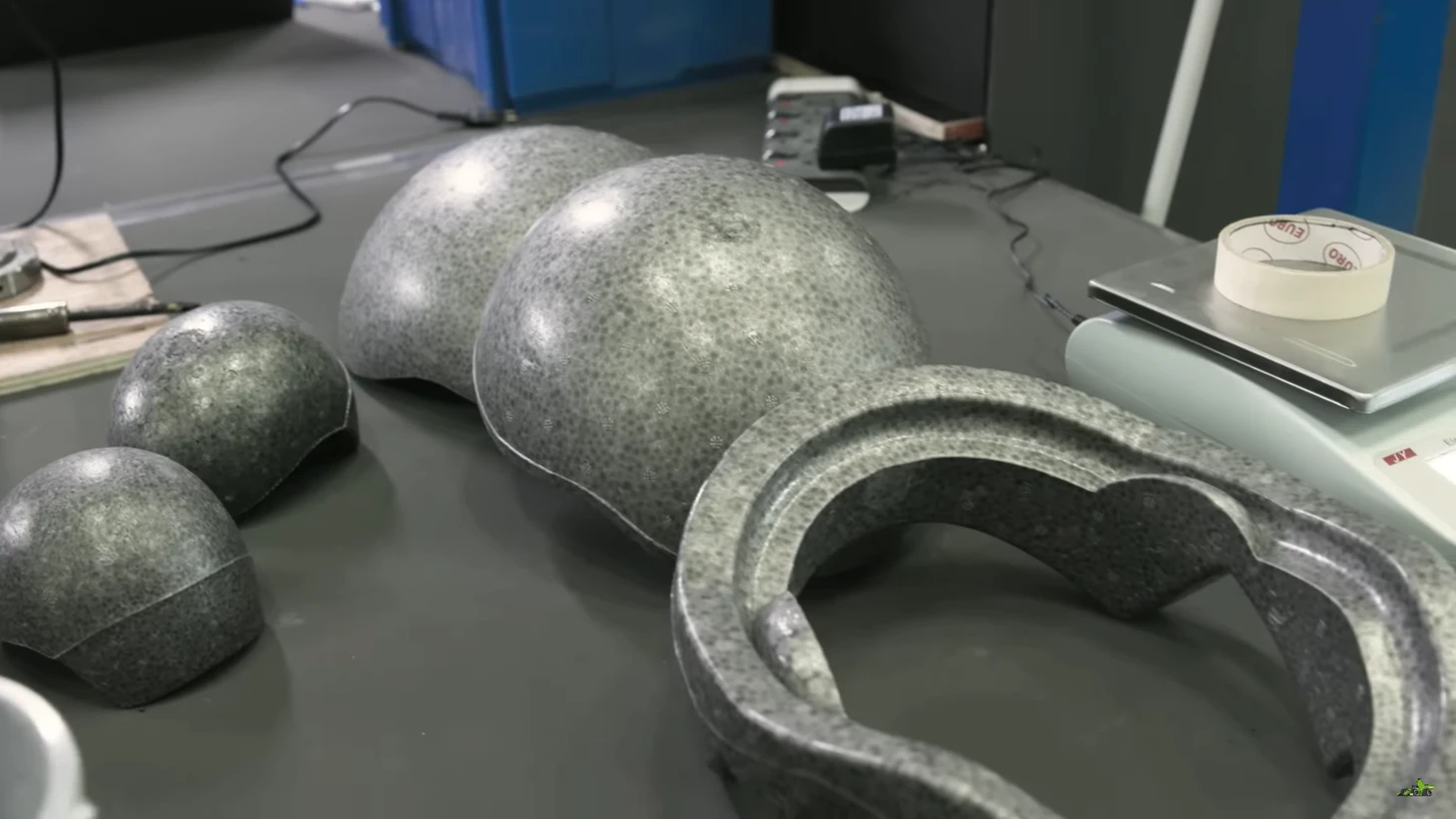
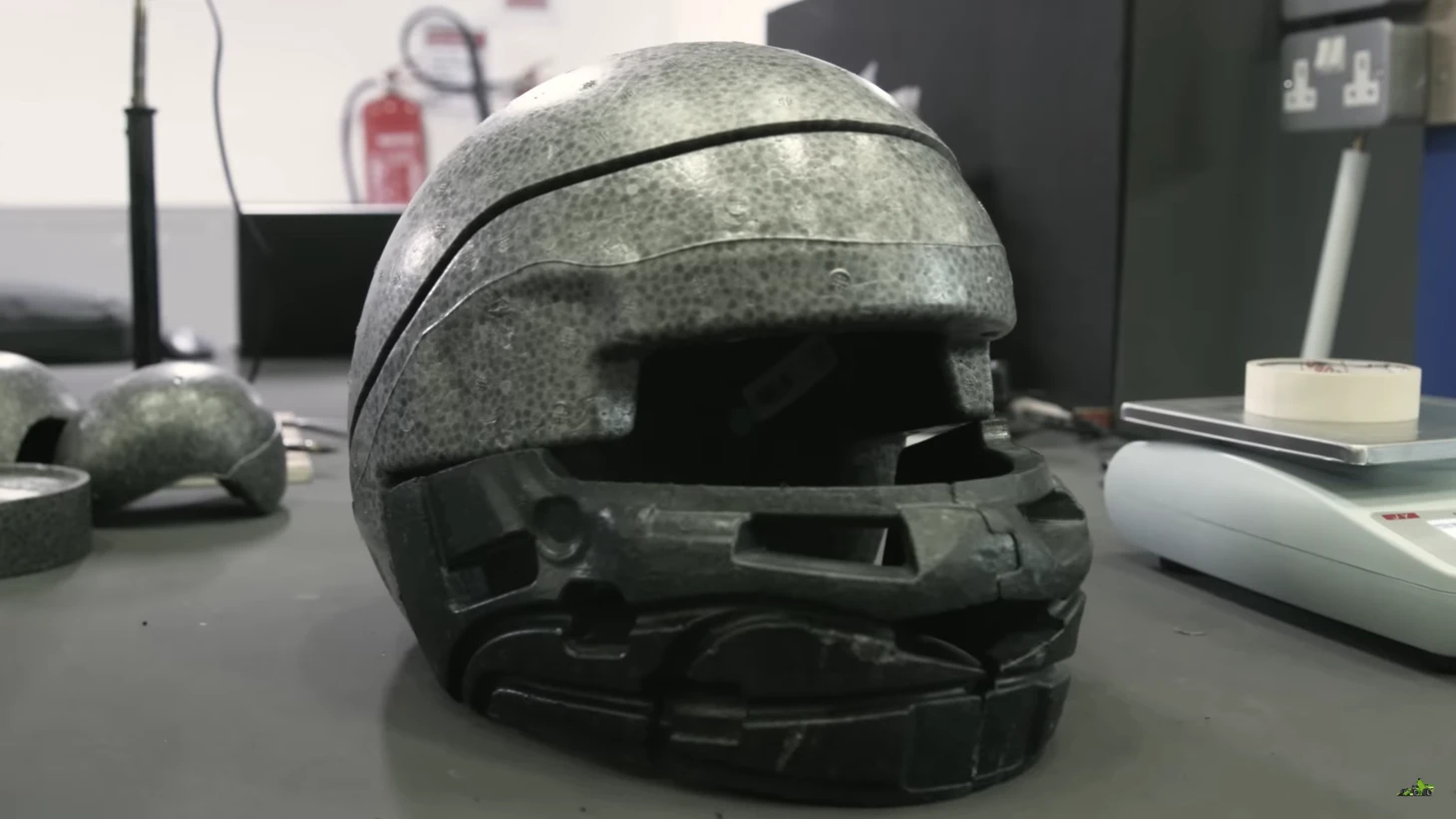
На ощупь готовый материал похож на слипшийся попкорн. Этот слой и поглощает энергию удара до того, как она доходит до головы пилота.
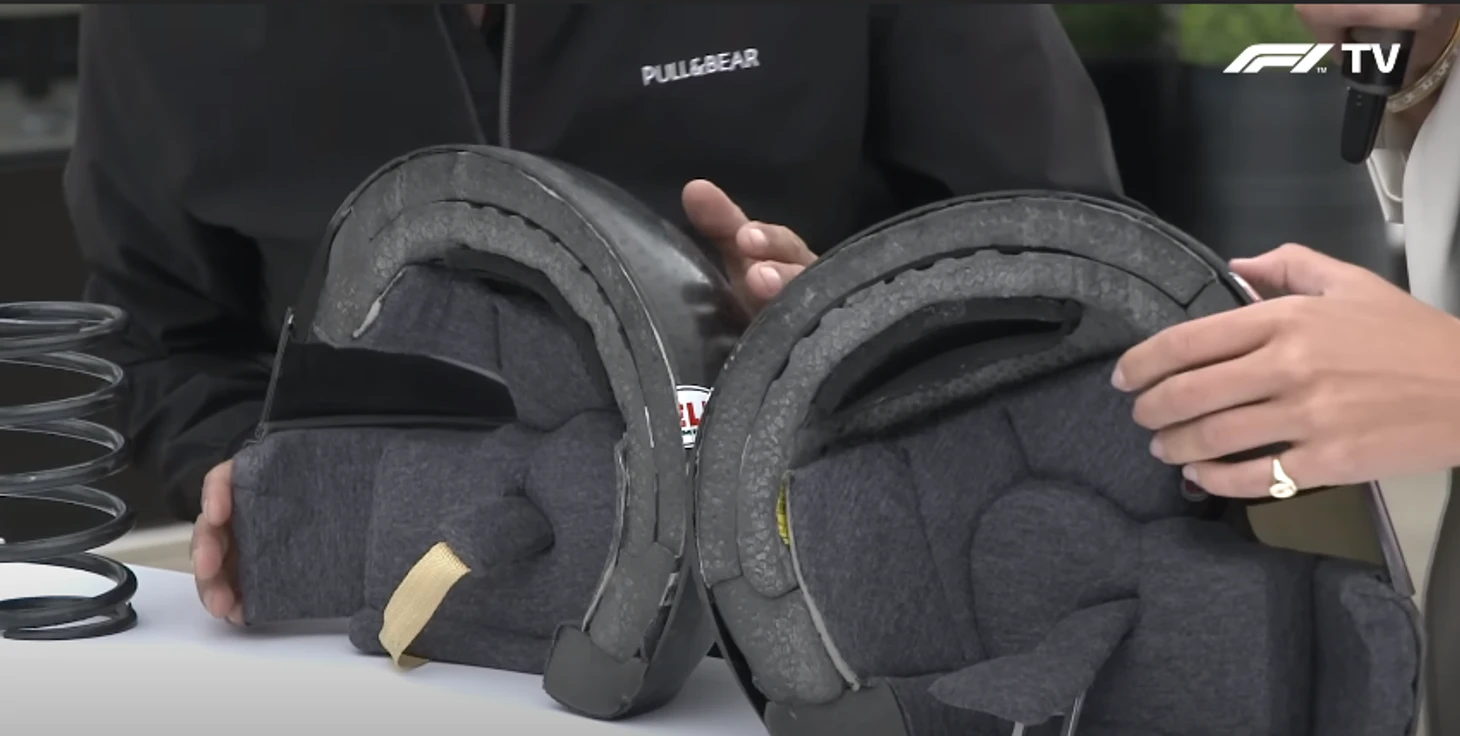
В этом же отделе производят пластиковые крепления для шлема. Интересный факт: все пластиковые отходы, образовавшиеся при заливке форм, перерабатывают и вновь используют в производстве.
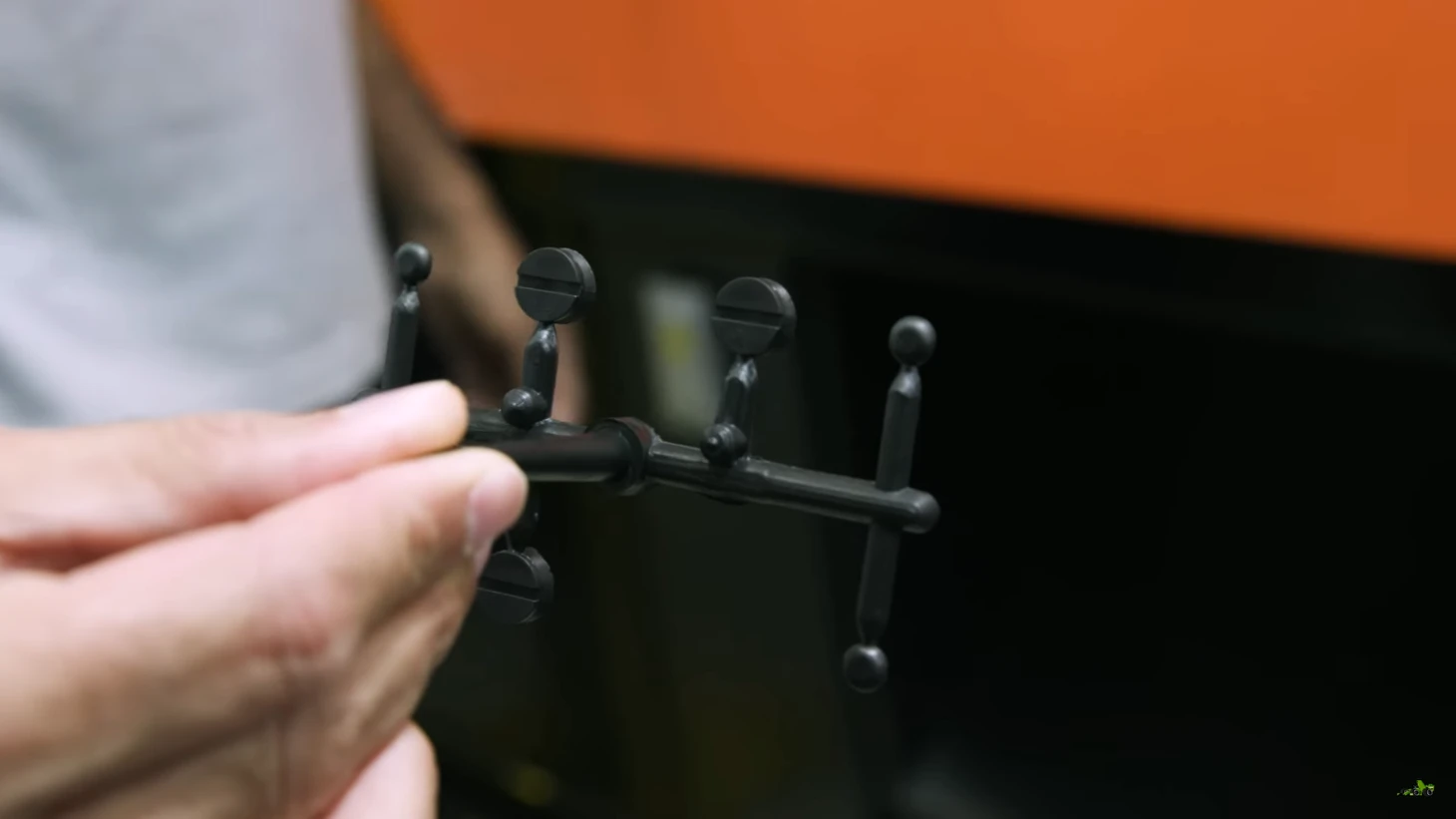
Следующий – отдел «электроники». Здесь в шлемы упаковывают всю современную электронику: от проводов гоночного радио до новинки: мини-камер, показывающих в трансляции вид от первого лица.

Наружную «ракушку» изготавливают в отделе «нарезки и хранения препрегов» (это полуфабрикаты из композитов).
Здесь специальный пресс нарезает карбоновые листы на элементы нужной формы, из которых и собирают оболочку.
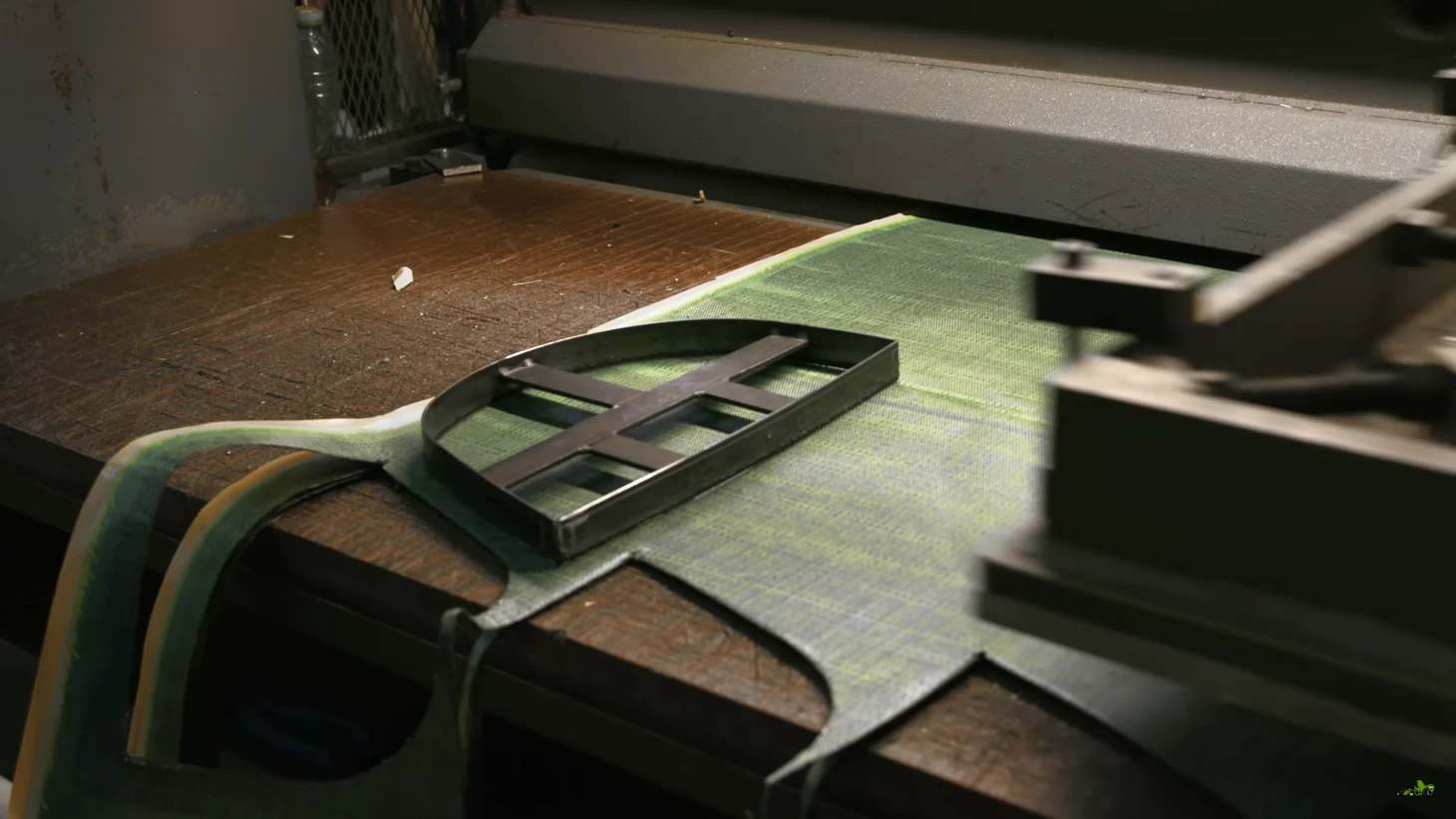
Но это не тот же карбон, что и у корпуса болидов: этот – особенно крепкий, конкретно для противостояния любым попыткам «пробития» от осколков и пружин.
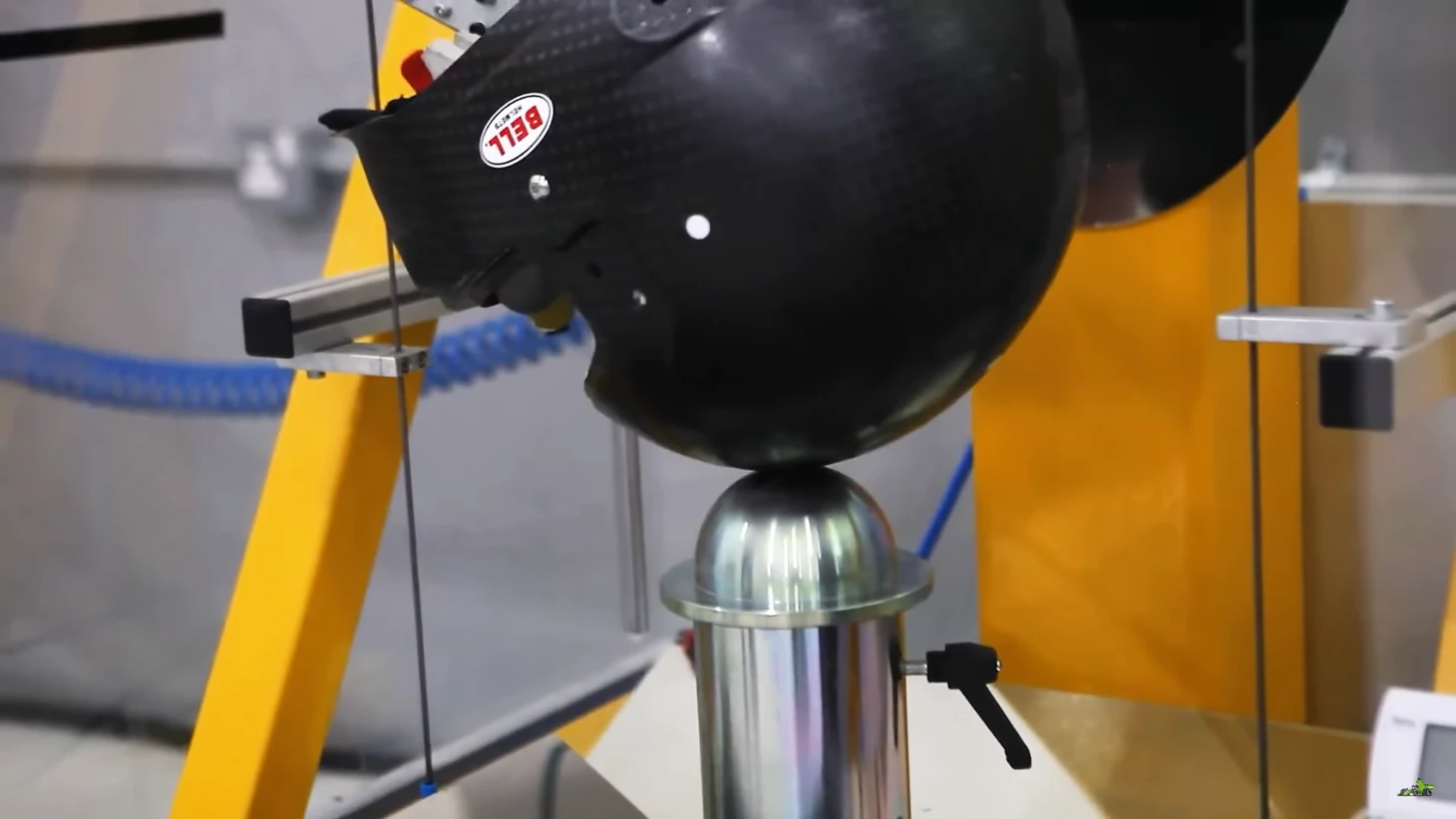
Его испытывают на специальном станке. Остроконечный груз весом 4 кг поднимают на высоту 4 м и сбрасывают на карбоновую «ракушку». Кроме этого, конструкция шлема должна выдерживать попадание 225-граммового предмета на скорости в 250 км/ч, падение 10-килограммового предмета с высоты 5,1 м.
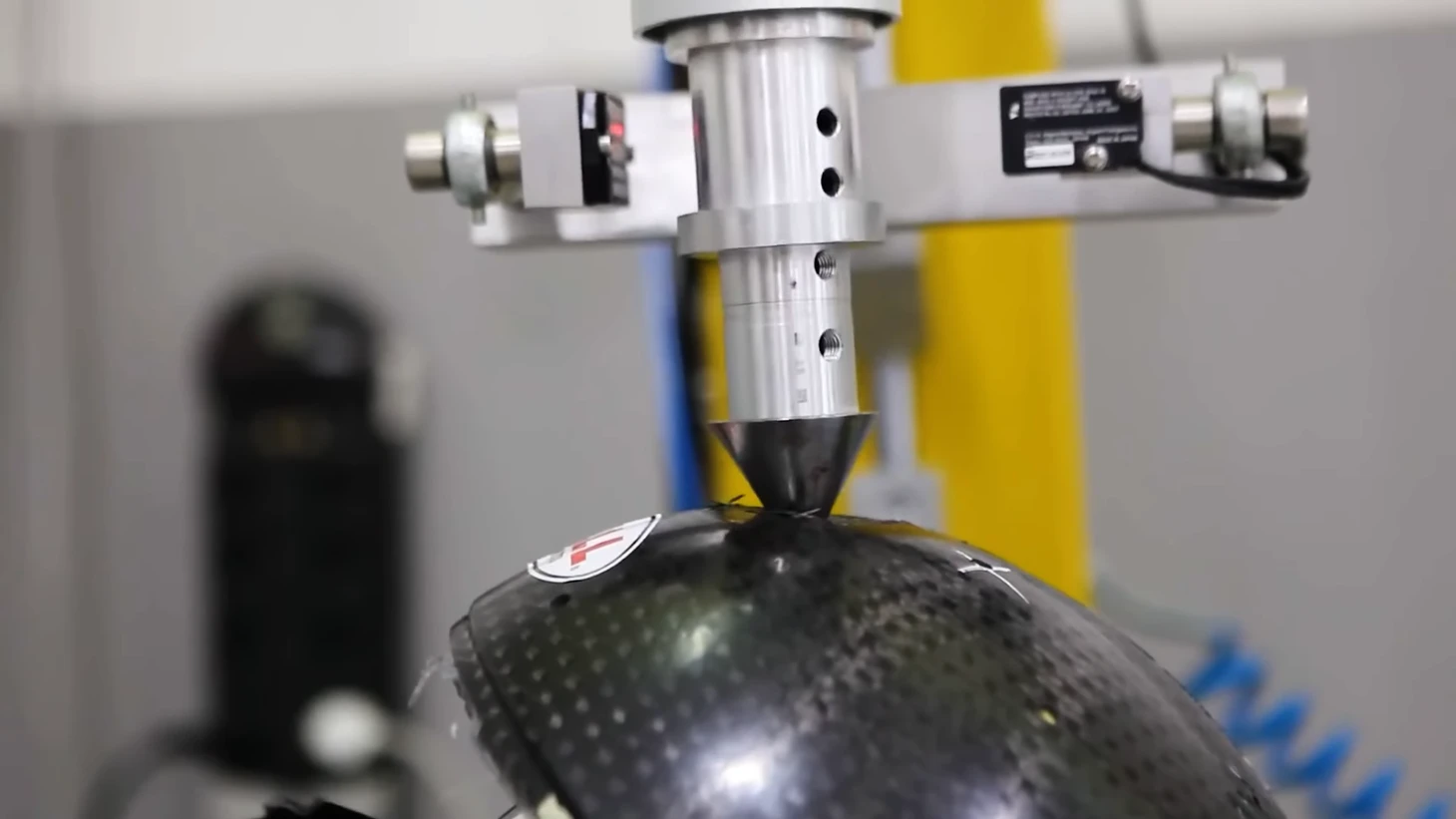
Шлем обязан без повреждений переносить воздействие открытого пламени температурой 790 градусов Цельсия, а стекло визора – отражать выстрел дробью массой 1,2 грамма из пневматического ружья. Полный документ требований ФИА к тестам и безопасности для получения лицензии – 38 страниц!
Потому инженеры разработали 17 составов углепластика специально для гоночных шлемов! Но обычно конкретный тип из них выбирает команда с учетом необходимых свойств для аэродинамики. Над ними работали 10 лет.
«Эти материалы – очень, очень дорогие, лист стоит 150-180 евро за квадратный метр, – рассказывал глава конкурирующего производителя Schuberth Альберто Даль’Ольо. – И объем нужных материалов на рынке крайне ограничен. Почти весь выгребается самими командами и аэрокосмической промышленностью, мы буквально сражаемся за него».
Почему не пользуются алюминием? Он сильнее расширяется при нагревании и теряет ту же температуру за 4 часа, что карбон за 10 минут. Победа нокаутом в смысле жаростойкости.
На один шлем в среднем уходит пять квадратных метров. 8 мм толщины всевозможных версий продвинутых углепластиков.
Они настолько капризные и требовательные, что даже хранить их нужно в особых холодильниках: например, марка T1000 для монококов болидов «Ф-1» требует только диапазона от -15 до -20 по Цельсью до цикла производства, а при иных температурах быстро «активируется» – либо делаешь деталь сразу, либо выбрасываешь. А выпекать их в форме нужно только при температуре 126 градусов – ошибка хотя бы на 0,2 градуса по Цельсию портит всю партию.
Процесс исследования и разработок материалов настолько секретный, что одно из условий посещения баз любого производителя – не снимать там. Ничем, даже телефоном.
В отделе «ламинирования» оператор покрывает ладони специальным термозащитным гелем, а затем разглаживает эти вырезки по разогретым формам. При нагревании карбоновые листы становятся более податливыми, что позволяет избавиться от складок на изделии при распределении его по форме.
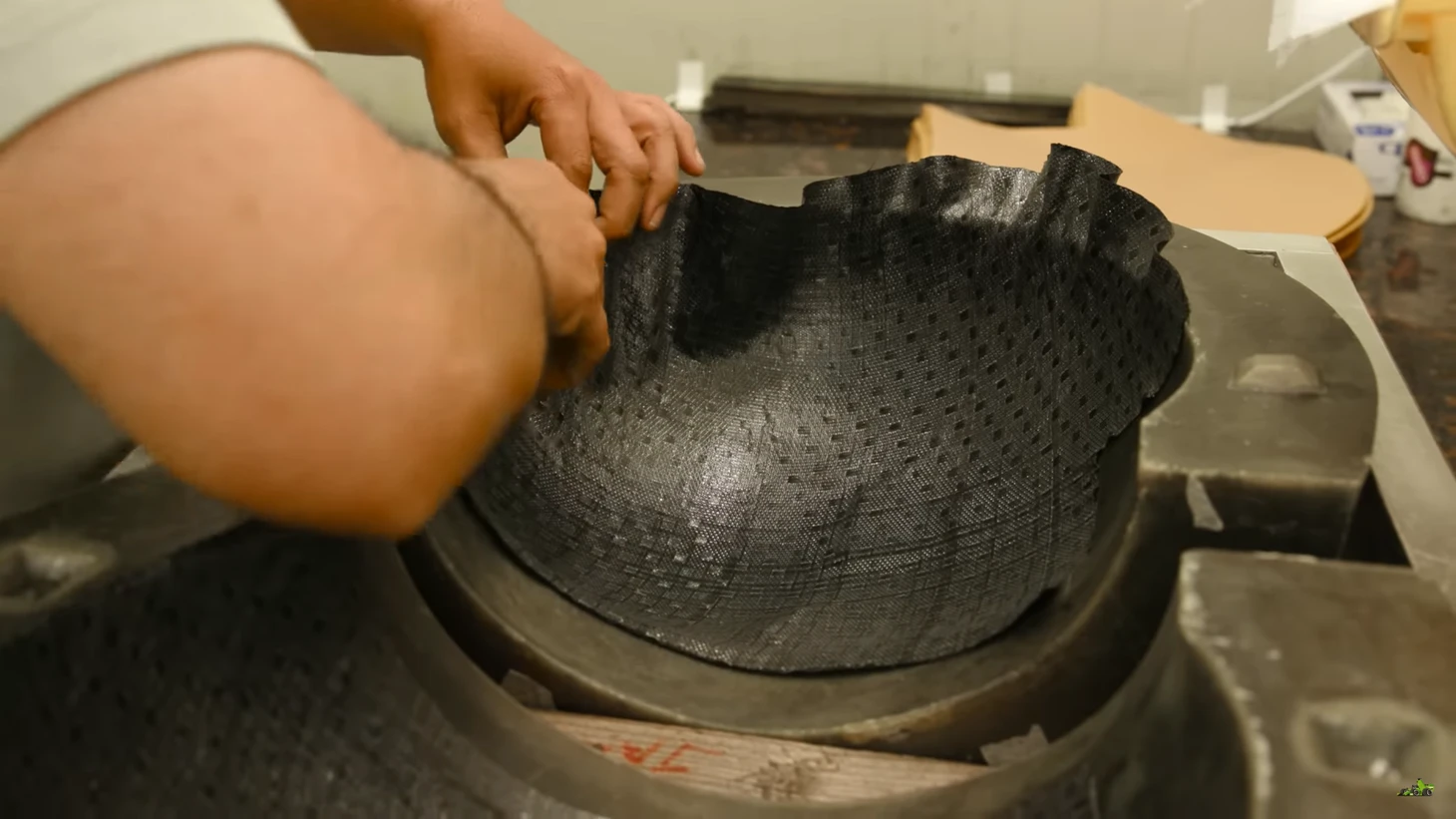
Да, в каждом шлеме гонщика «Ф-1» – огромная часть ручной работы!
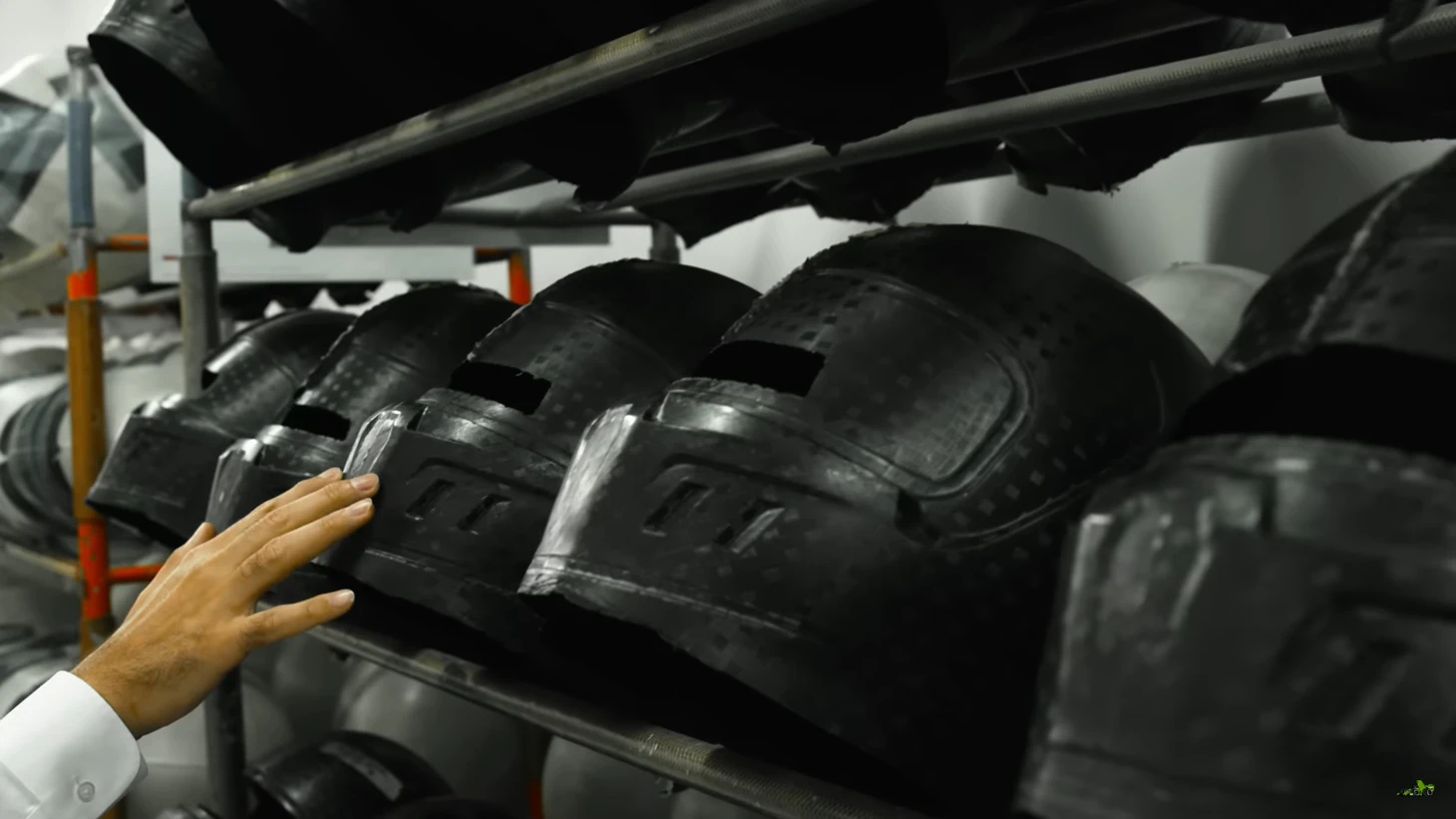
Отсюда готовая «ракушка» отправляется в отдел «обрезки и сверления». Здесь срезают все излишки материала и вырезают отверстие под визор.
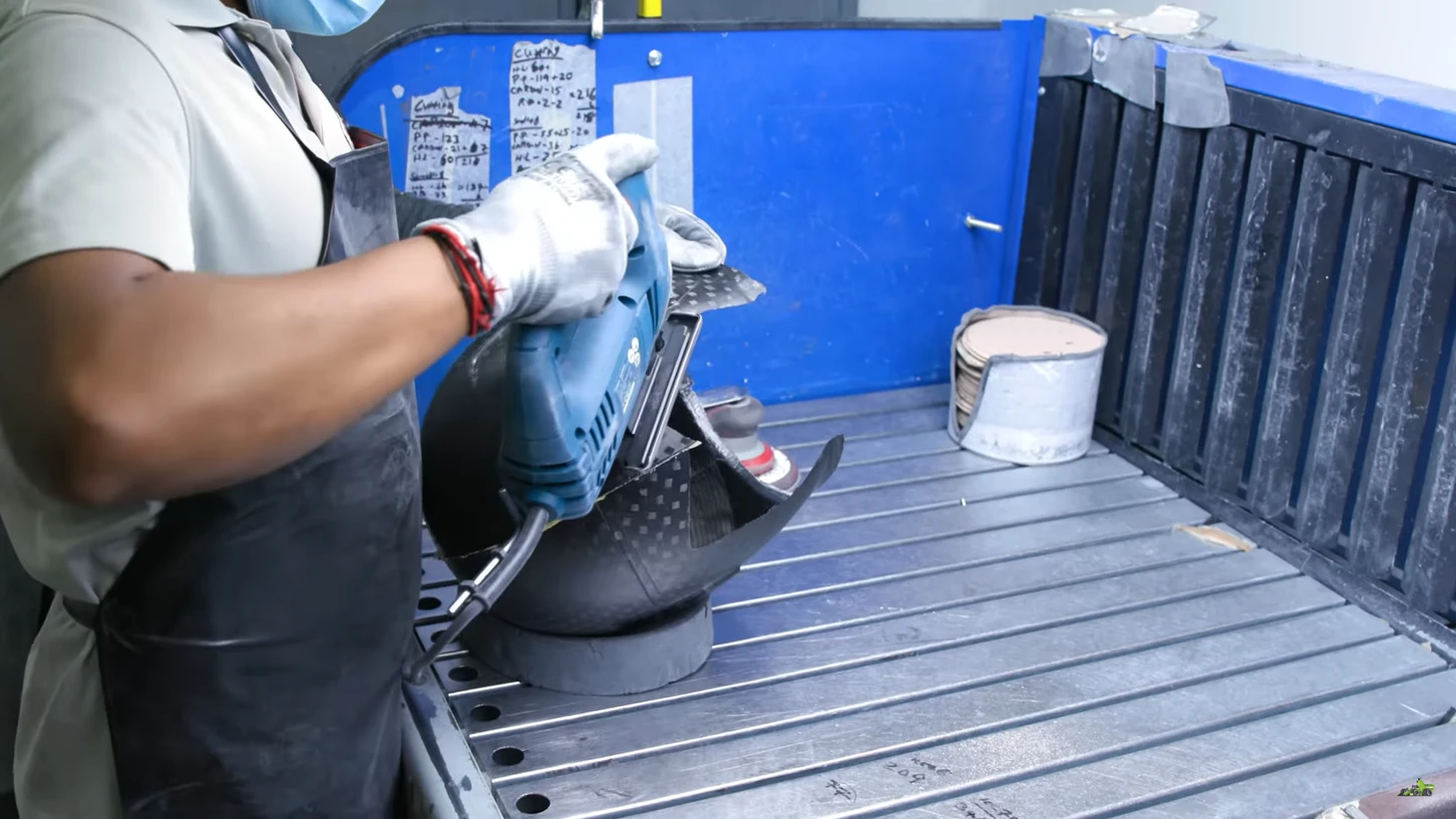
Затем при помощи специального шаблона прорезают в шлеме вентиляционные отверстия и отверстия для крепления визора.
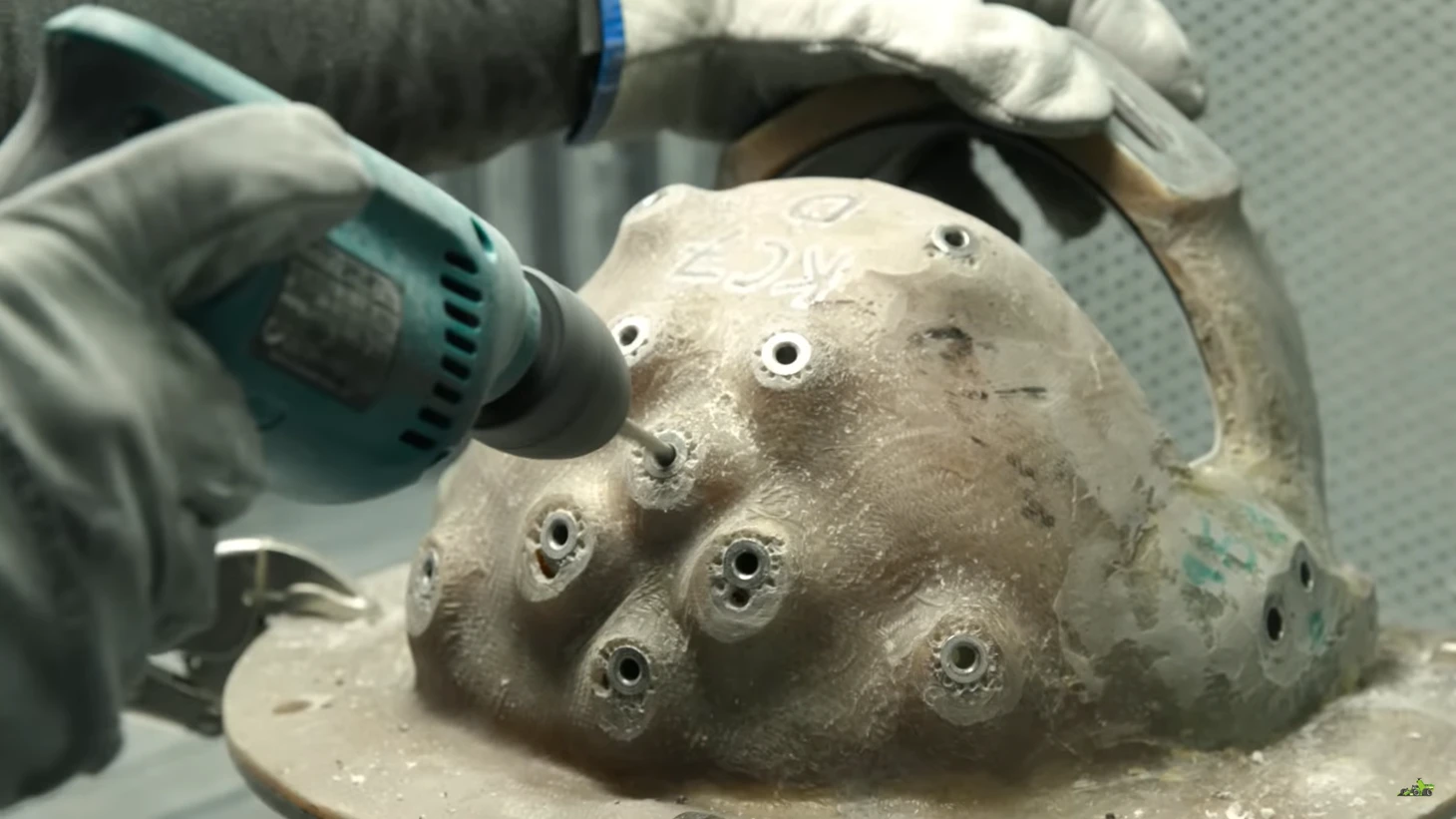
Перемещаемся в отдел «шлифовки и грунтовки». Название департамента говорит само за себя. Все излишки и неровности спиливают, а щели и дыры замазывают филлером.
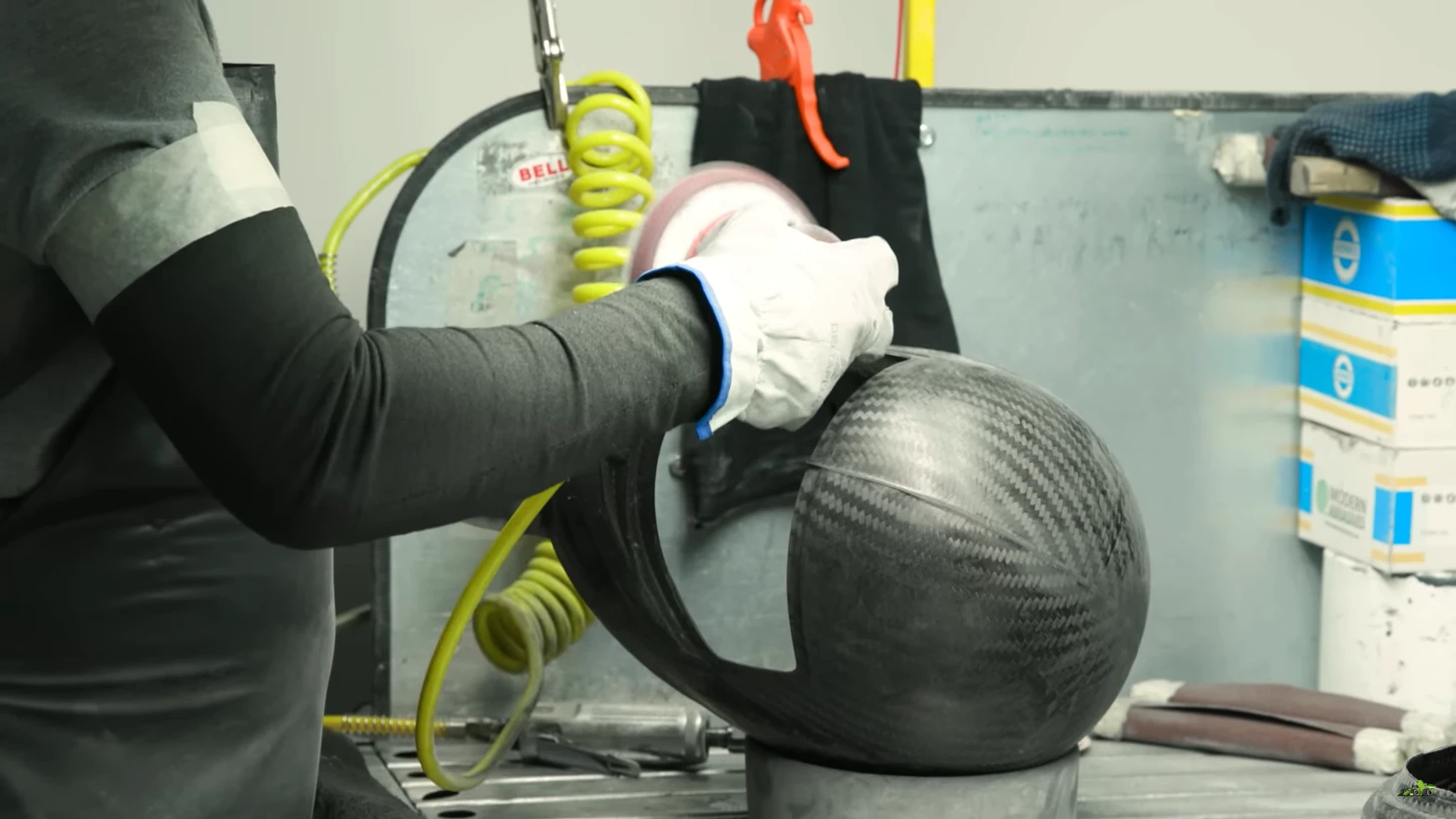
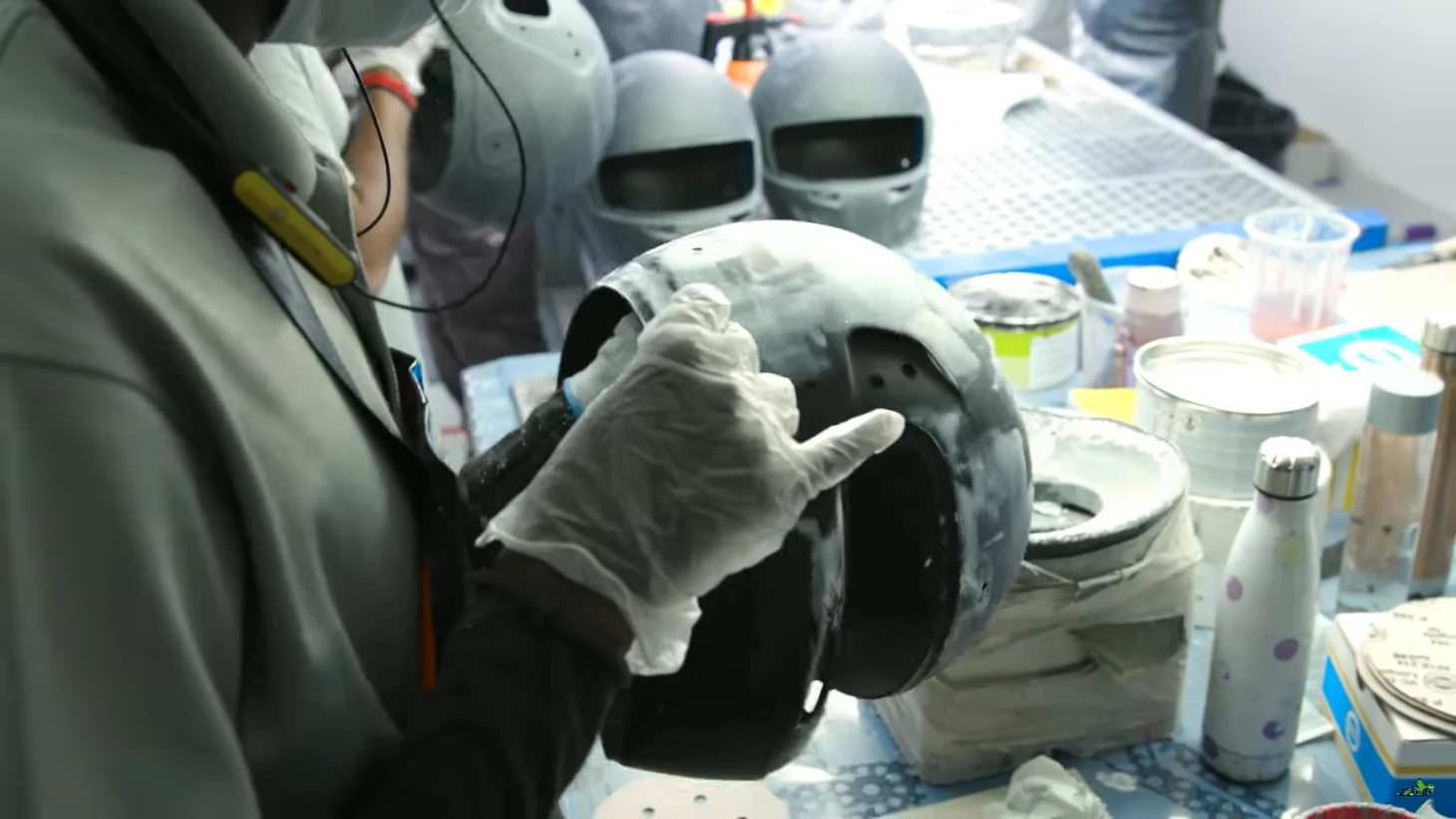
Остается покрыть изделие праймером (основа для нанесения краски) и отправить на покраску в соответствующий отдел.
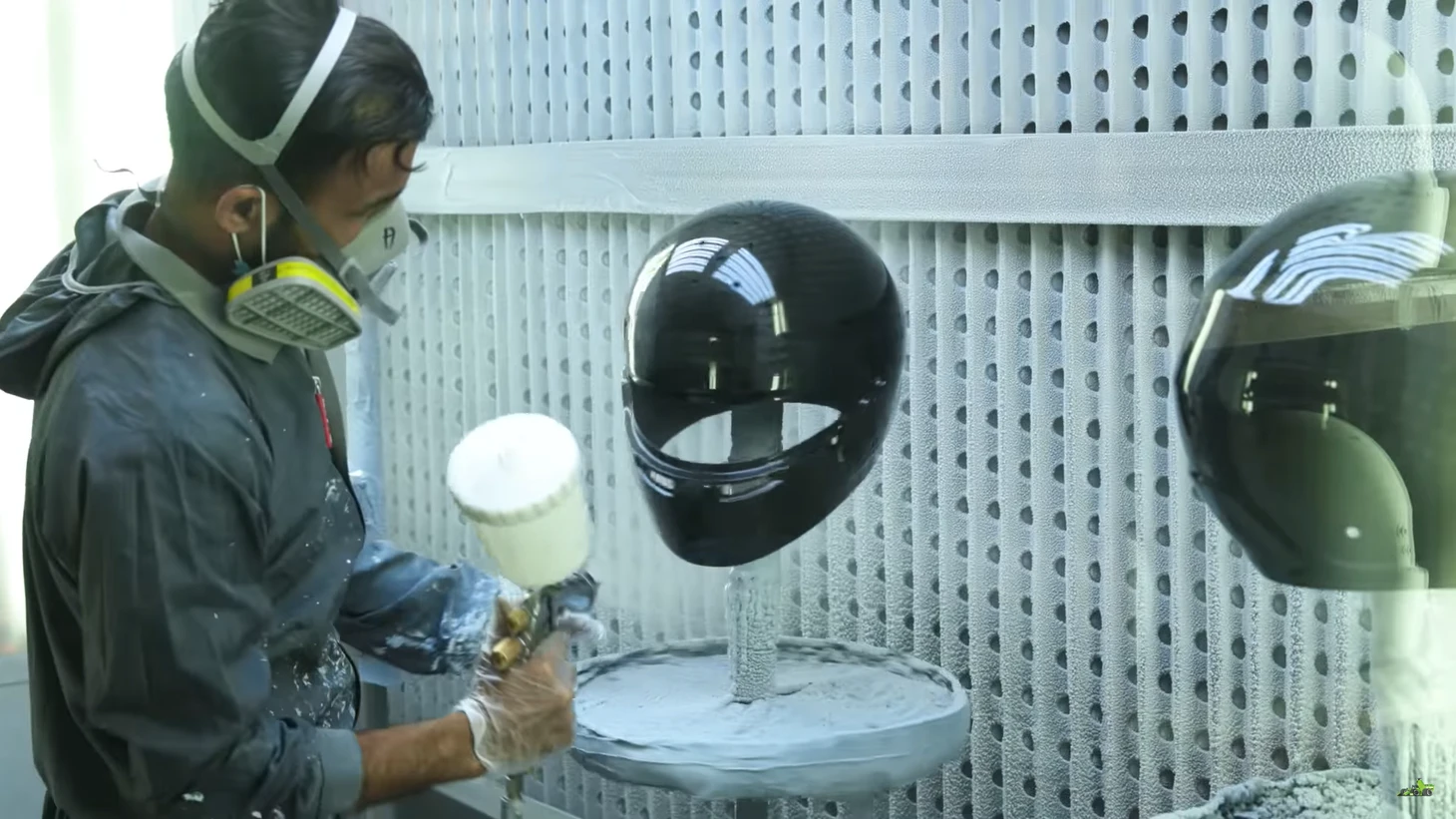
Здесь шлемы украшают виниловыми стикерами. Этот процесс похож на наклеивание на тело переводных тату.
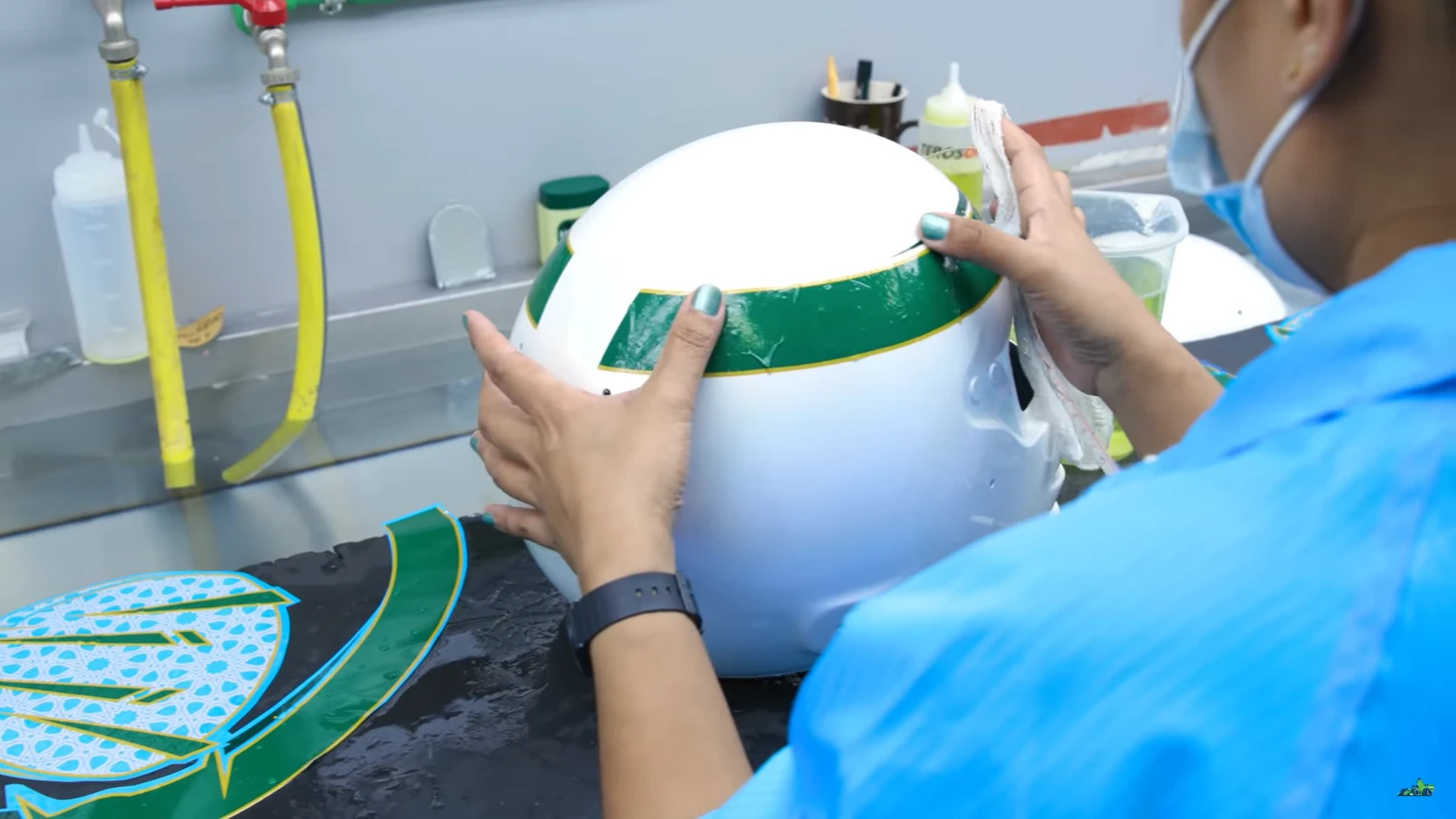

И наносят на защиту дизайны пилотов «Ф-1».

Наконец мы добрались до последнего отдела, он так и называется «финальная сборка». Его работники шьют ремешки из жаропрочного материала, а затем прячут их в слое пены, чтобы сделать комфортными для гонщиков.
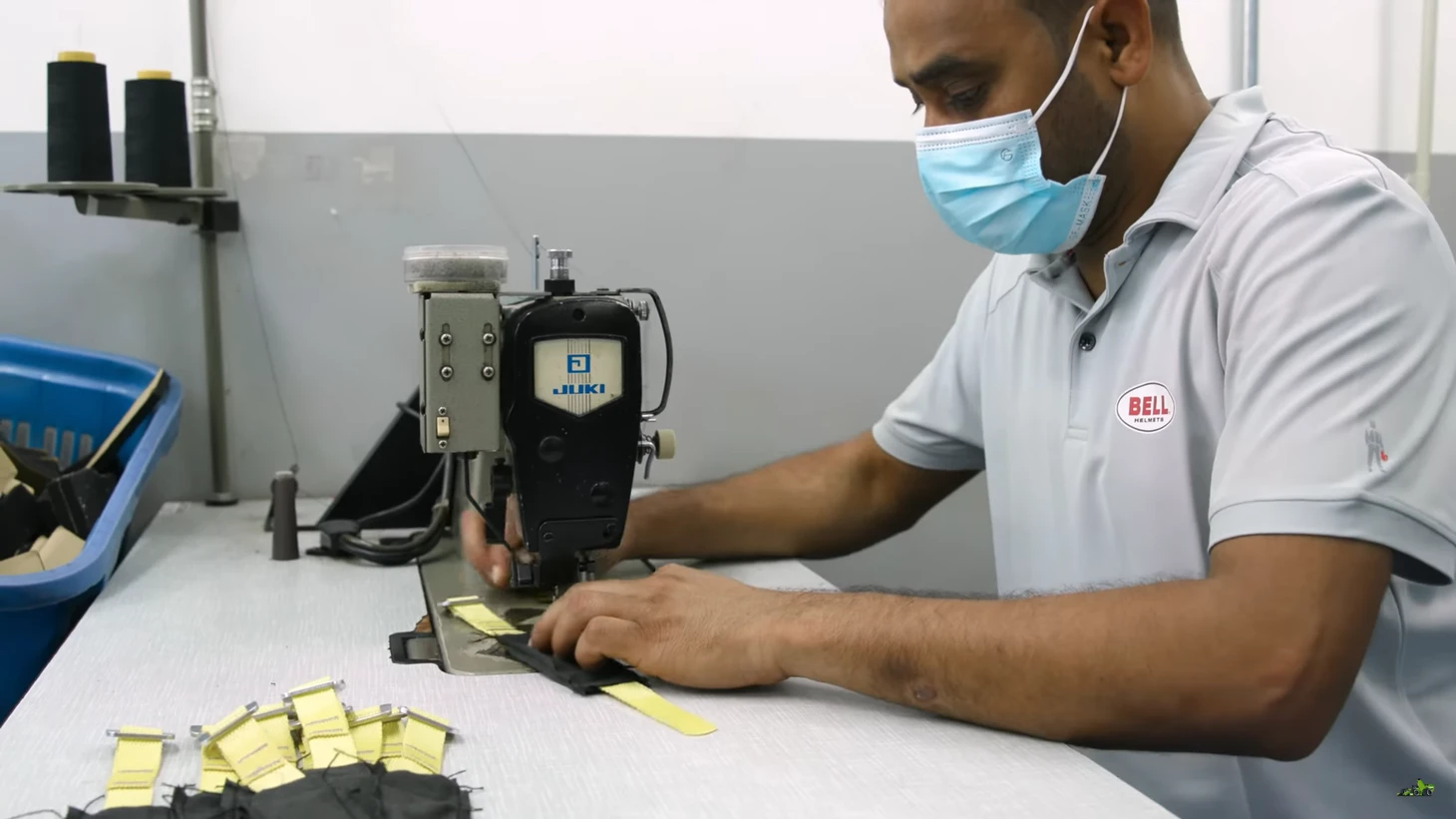
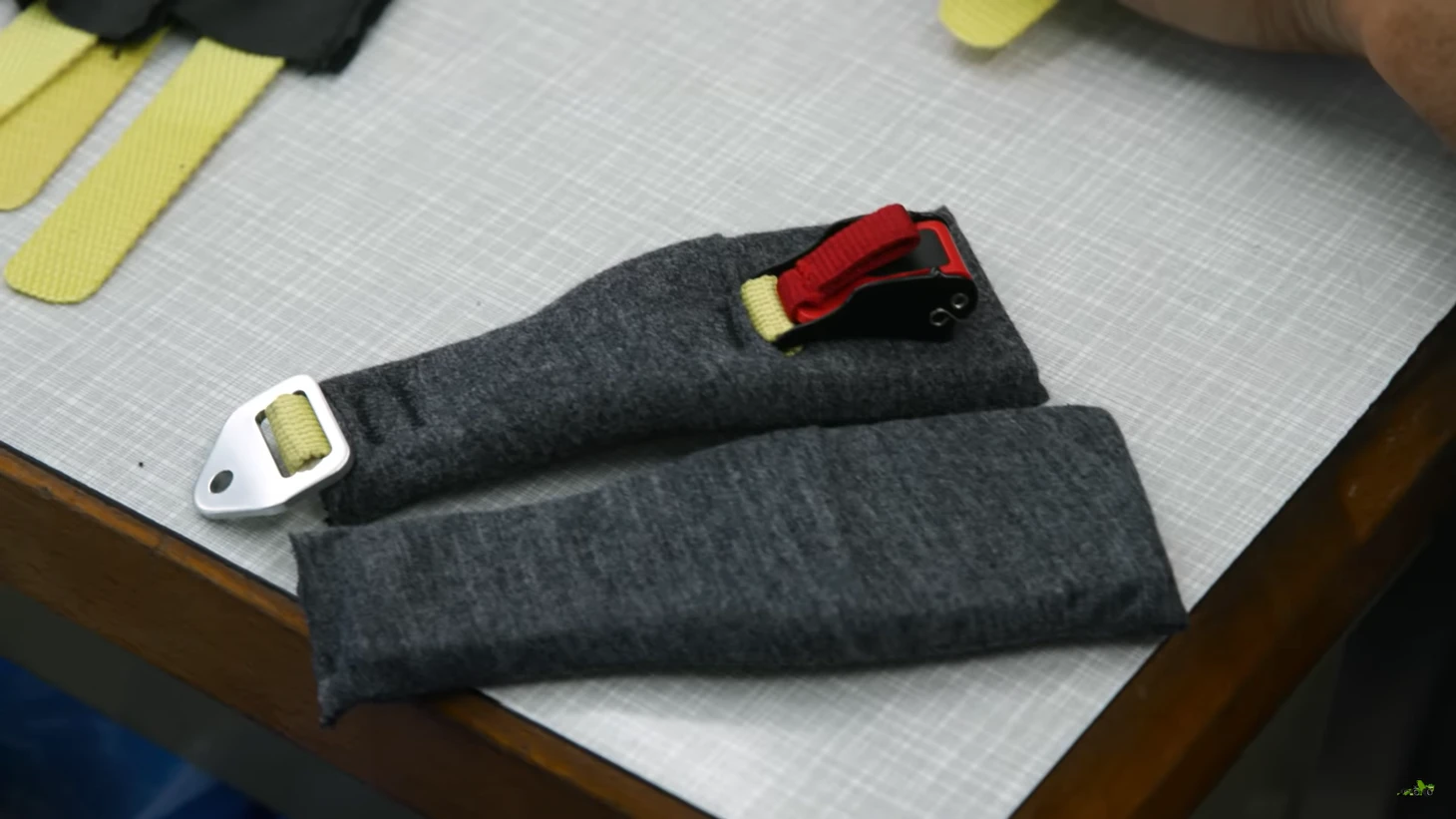
Пеной и негорючим материалом оборачивают все внутренности шлема, чтобы сделать их комфортными для гонщиков. В некоторых деталях так же оставляют прорези для того, чтобы команда могла упаковать в защиту необходимую электронику.
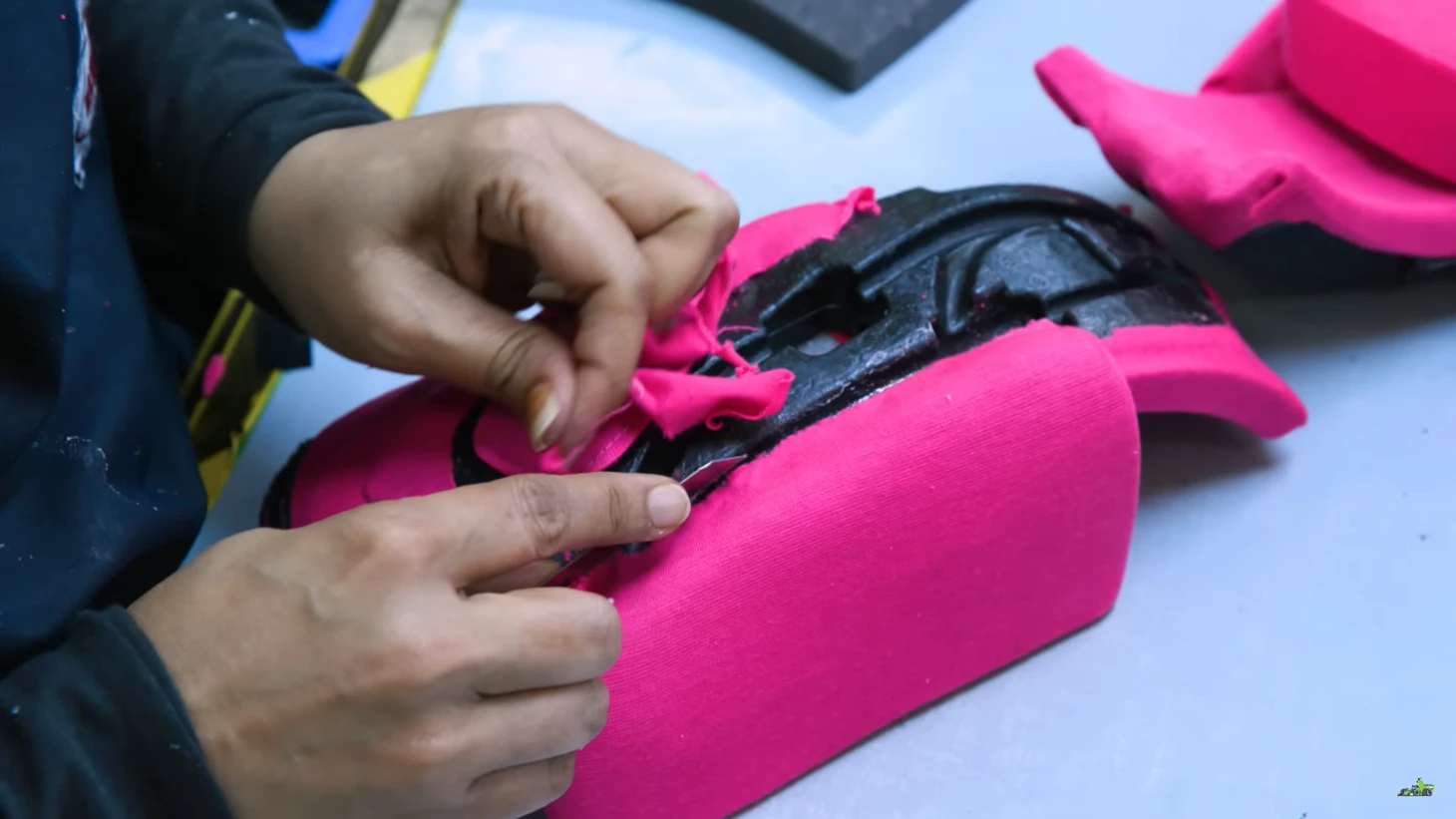
После того, как все детали подготовлены, можно начинать сборку шлема.
Сначала вентиляционные отверстия подчищают металлической щеткой, и наносят на них клей, чтобы закрыть кусочком металлической сетки, которая препятствует попаданию внутрь шлема мелкого мусора.
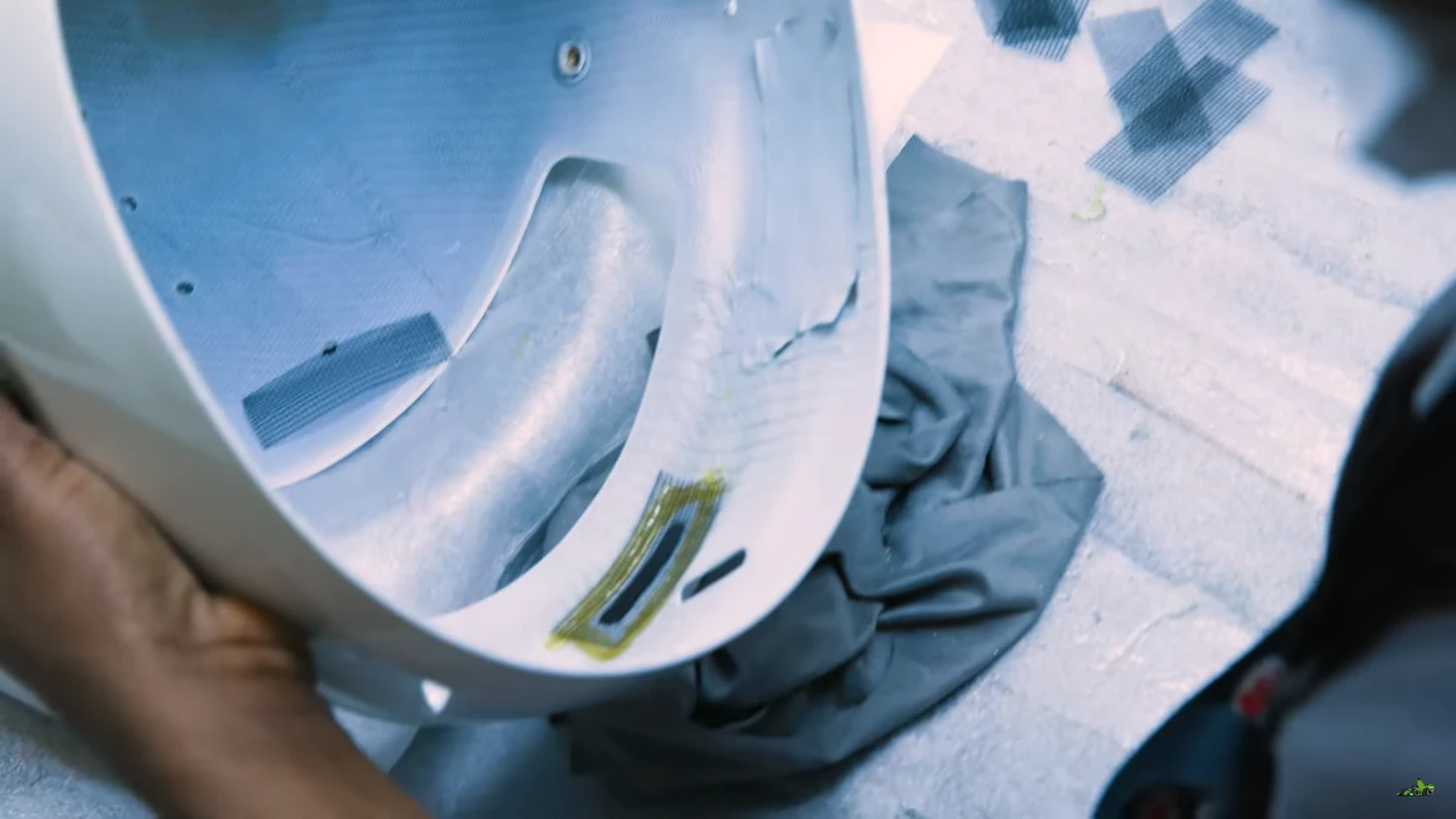
После низ шлема и края отверстия под визор обрамляют резинкой, чтобы смягчить их и обеспечить плотное прилегание забрала.
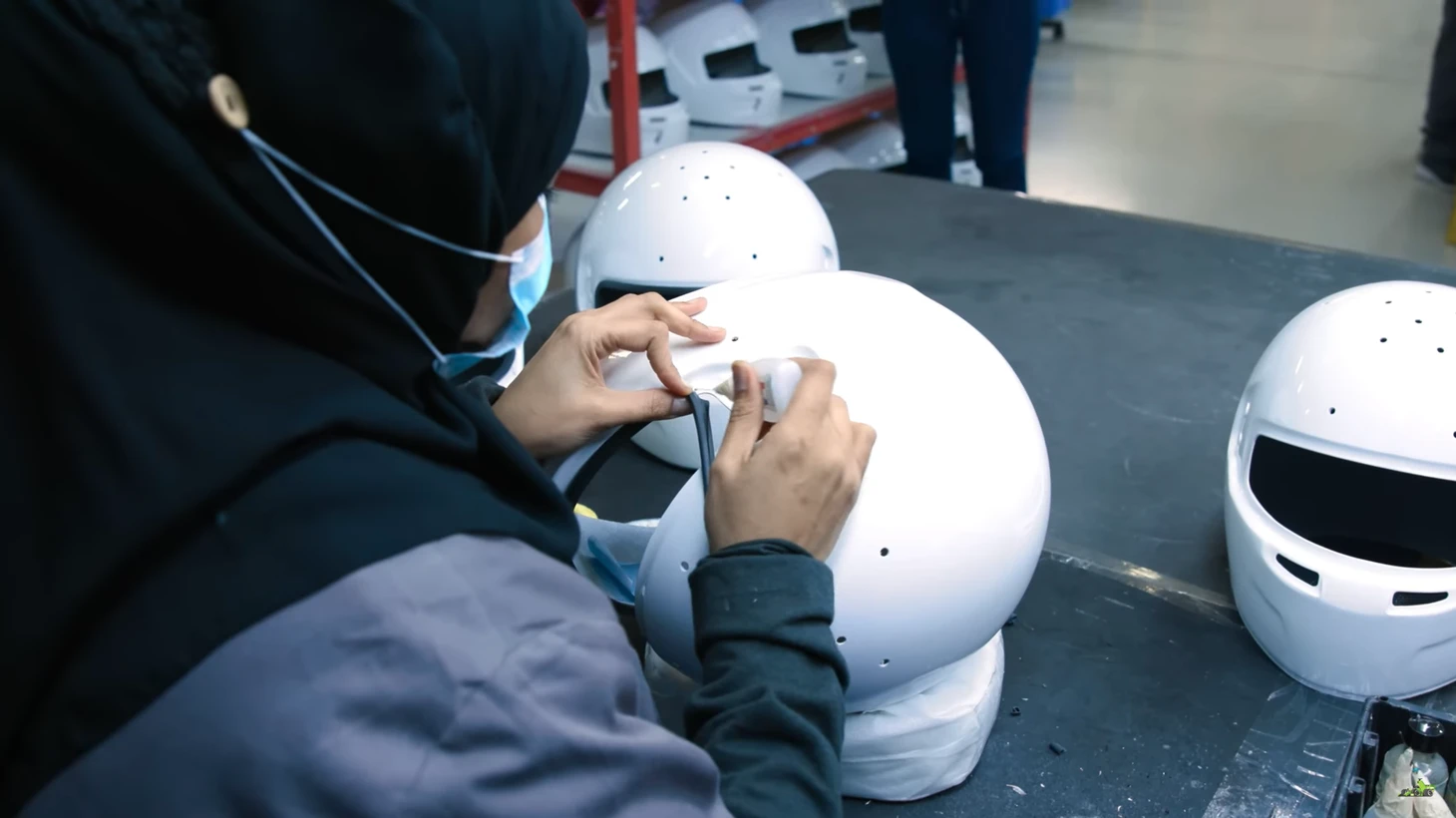
А затем внутренности наконец помещают внутрь «ракушки» при помощи вот такой обмотки. Она помогает работнику аккуратнее разместить части шлема, без нее оператор может нечаянно повредить клеевой слой на ткани.
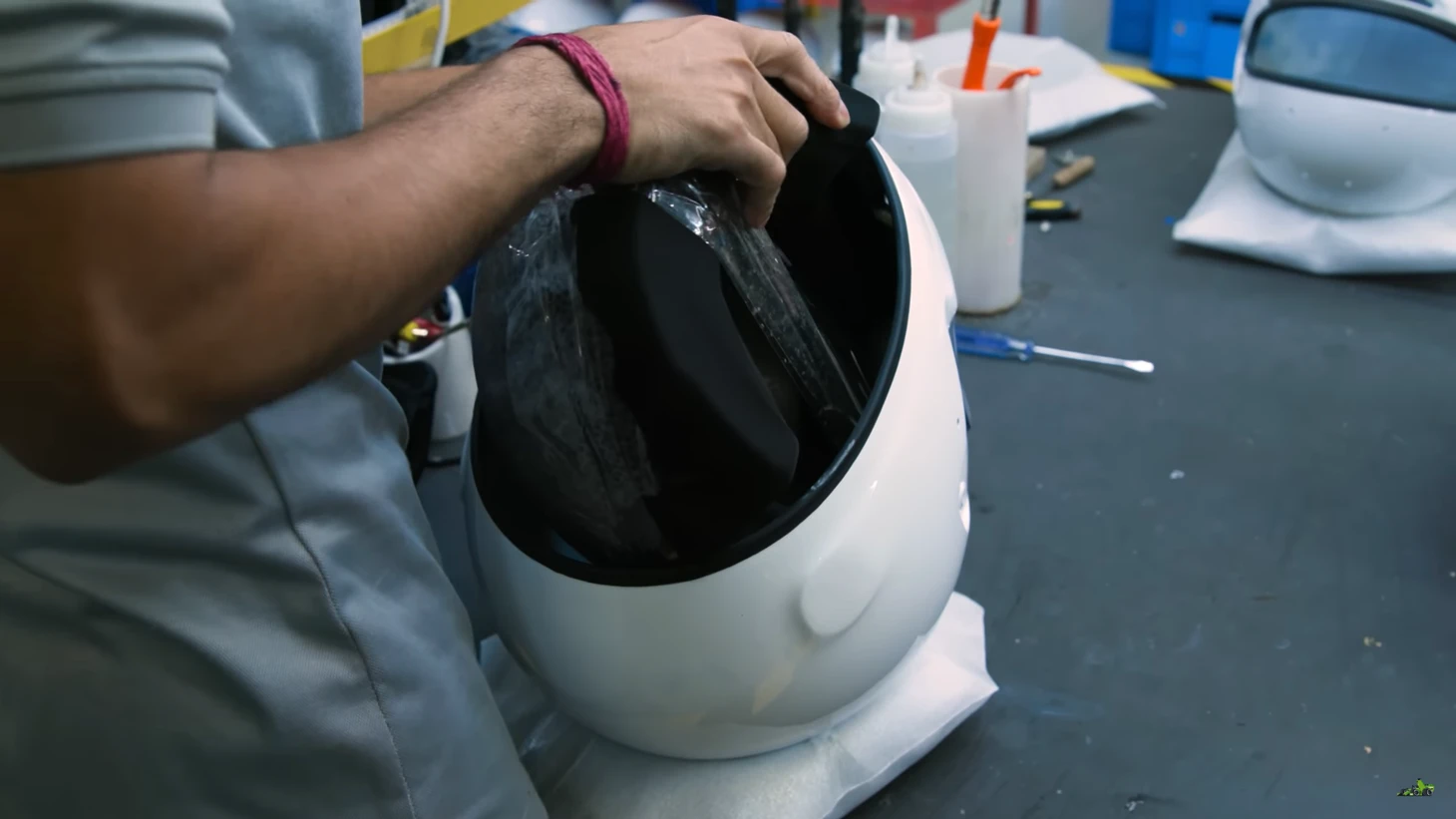
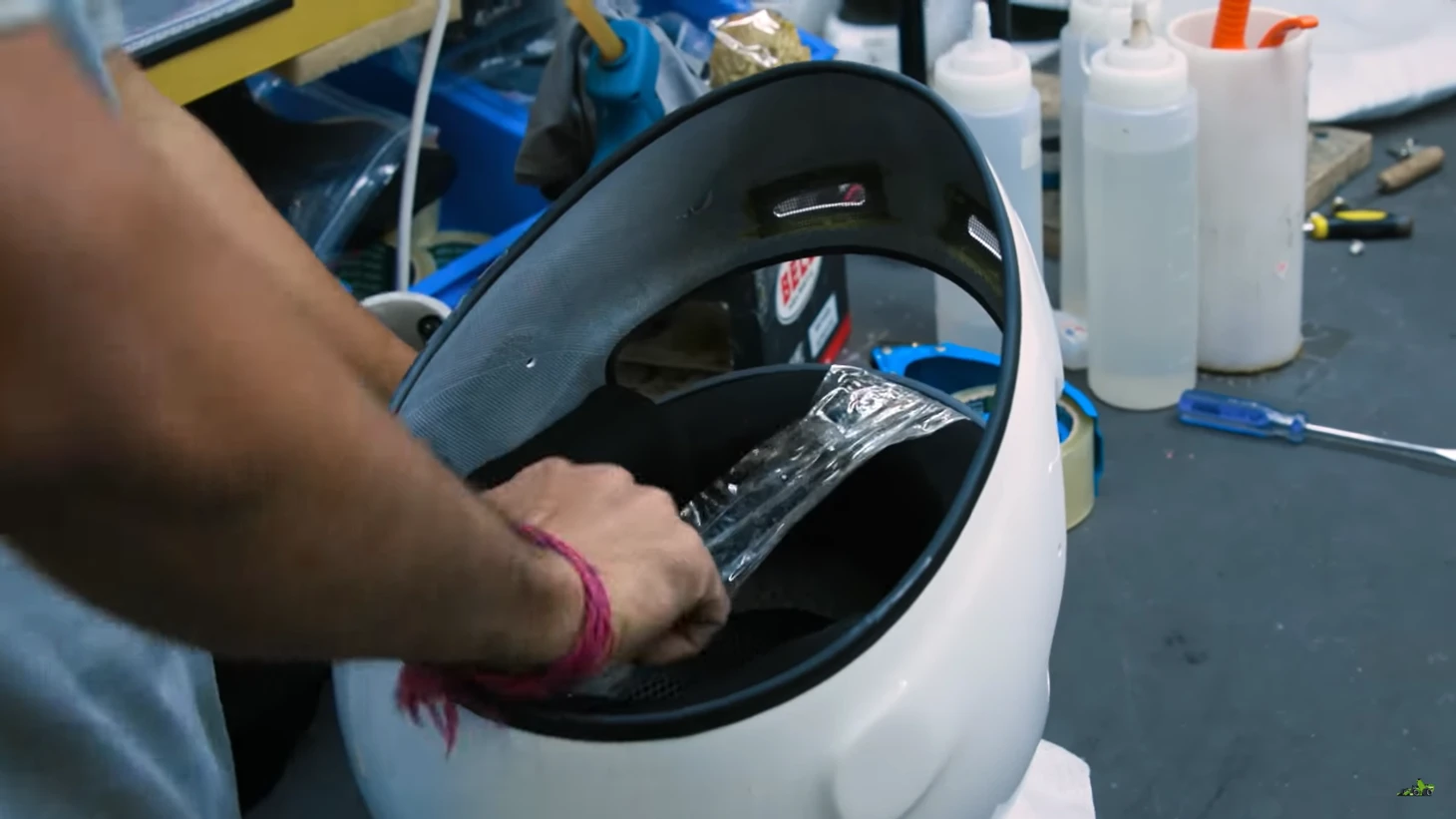
Последний этап – прикрутить визор. Это целая наука, ведь нужно убедиться, что пилоту будет удобно открывать и закрывать заслонку.
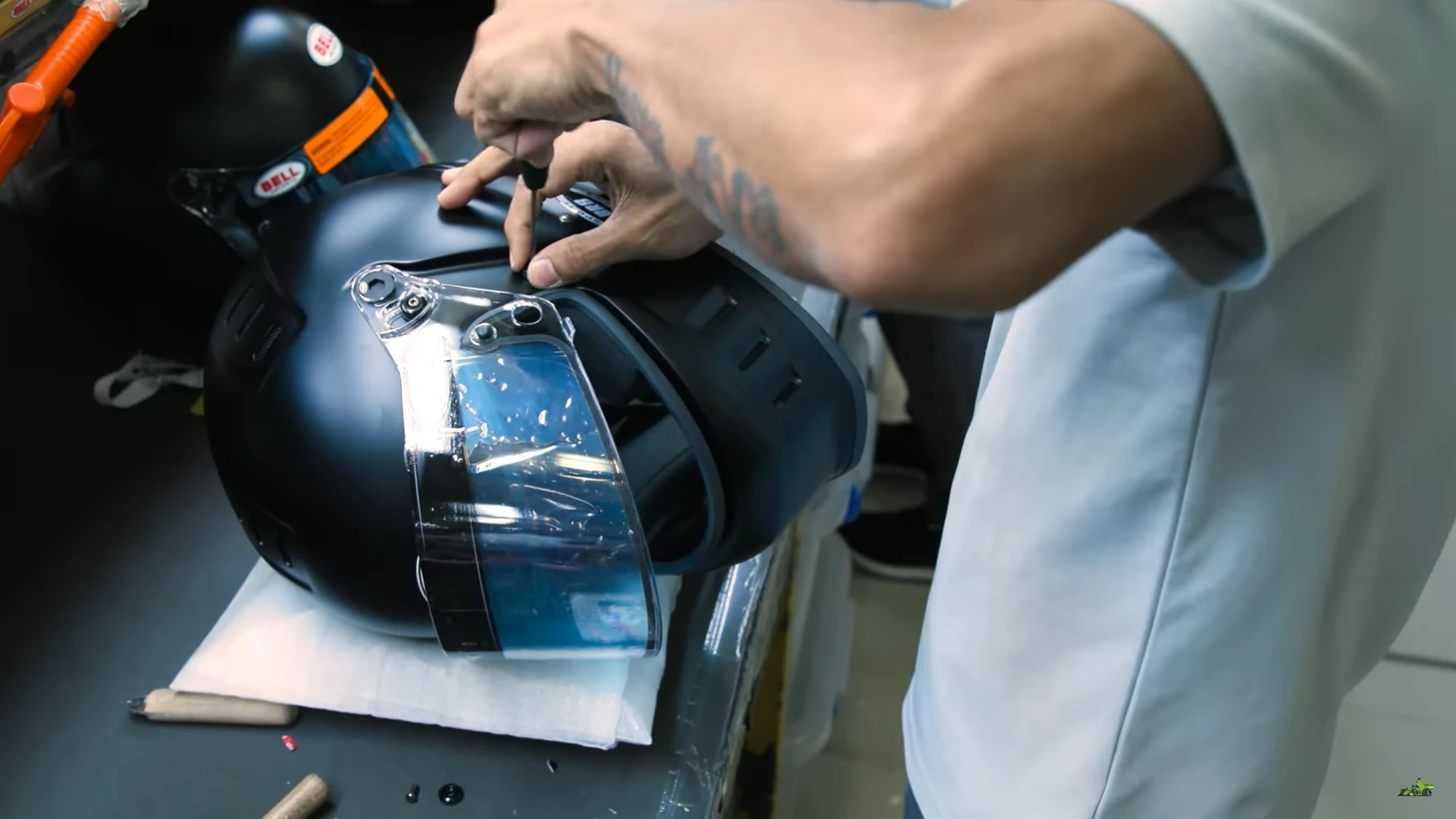
Остается лишь проверить качество готового изделия, упаковать по коробкам и разослать заказчикам. На сборку одного экземпляра с нуля уходит примерно 5 часов чистой работы.
Причем важна каждая деталь – гонщики и команды моментально замечают и пытаются подстроиться под любое изменение конструкции.
«Иногда они нам говорят: ой, шлем теперь на 30 граммов тяжелее, а что случилось?» – признался Даль’Ольо. Но обычно из партии отбраковывается только 5% - точность на заводах вполне подходящая «Ф-1».
Тут мне как инженеру, больше всего чертежи шлема интересны конечно.
Может также про комбез рассказать и обувь?
Кстати вес готового шлема в итоге какой?